Zentriermessung
Die präzise Zentrierung und Ausrichtung einer Linse ist ausschlaggebend für die Bildqualität des optischen Systems! Steile These: Aber was bedeutet Linsenzentrierung? Nun: Ein Zentrierfehler liegt dann vor, wenn die optische Achse der Linse mit einer gegebenen Referenzachse, z. B. dem Linsenrand, der Fassung oder der optischen Achse einer zweiten Linse, in Lage und Richtung nicht übereinstimmt. Er entsteht beim Fertigen, Verkitten, Kleben und Justieren von Linsen und Linsensystemen. Um die Zentrierung von Einzellinsen und Linsensystemen nach der Herstellung zu prüfen und direkt während der Fertigung zu optimieren, liefern die Produkte der OptiCentric®-Familie Lösungen. Dabei spielt es keine Rolle, ob der Prüfling einen kleinen oder sehr großen Durchmesser hat, sphärische, asphärische oder zylindrische Oberflächen aufweist und im visuellen oder infraroten Spektralbereich arbeitet.
Anwendungen
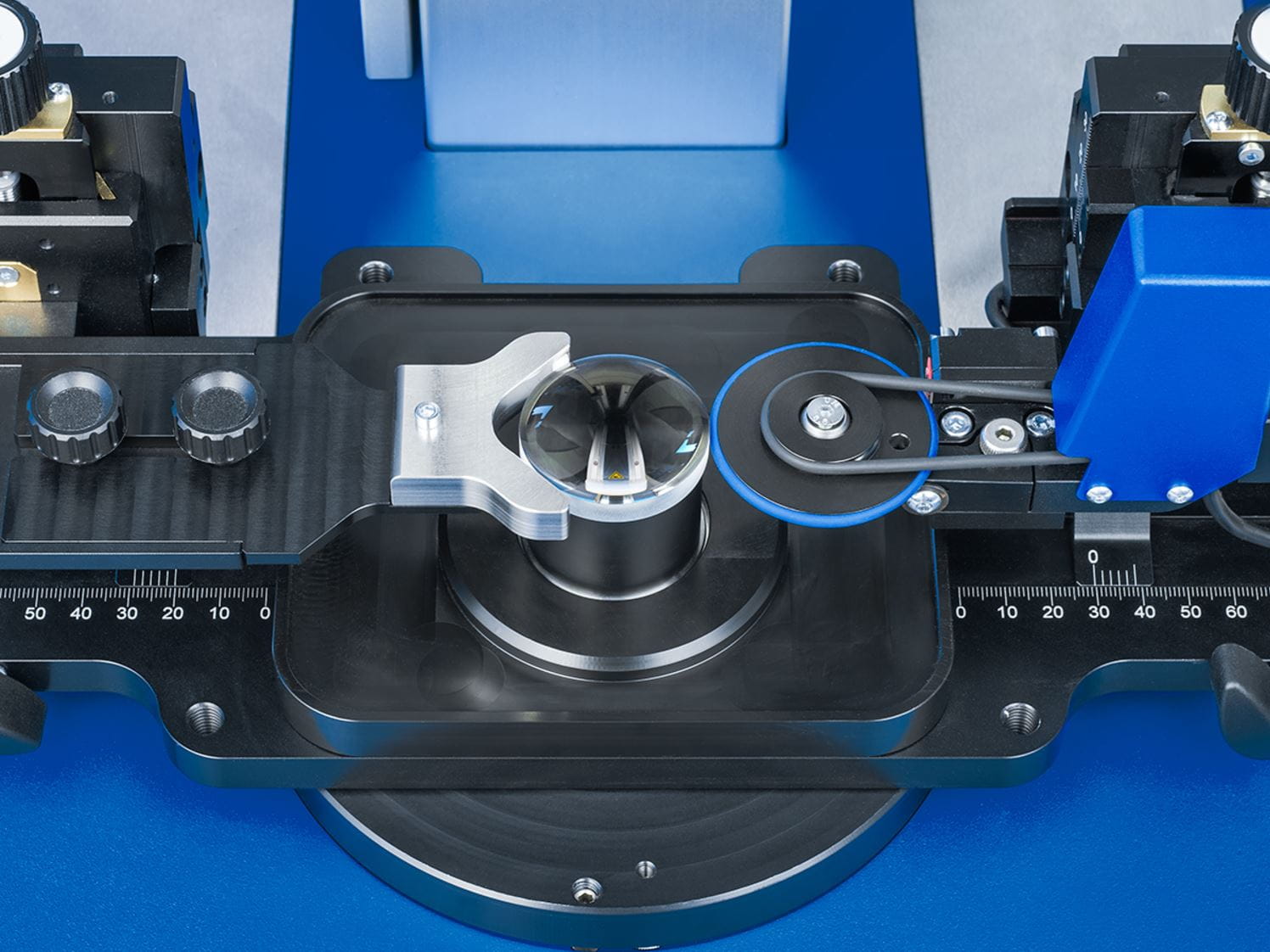
Zentrierprüfung von sphärischen Einzellinsen
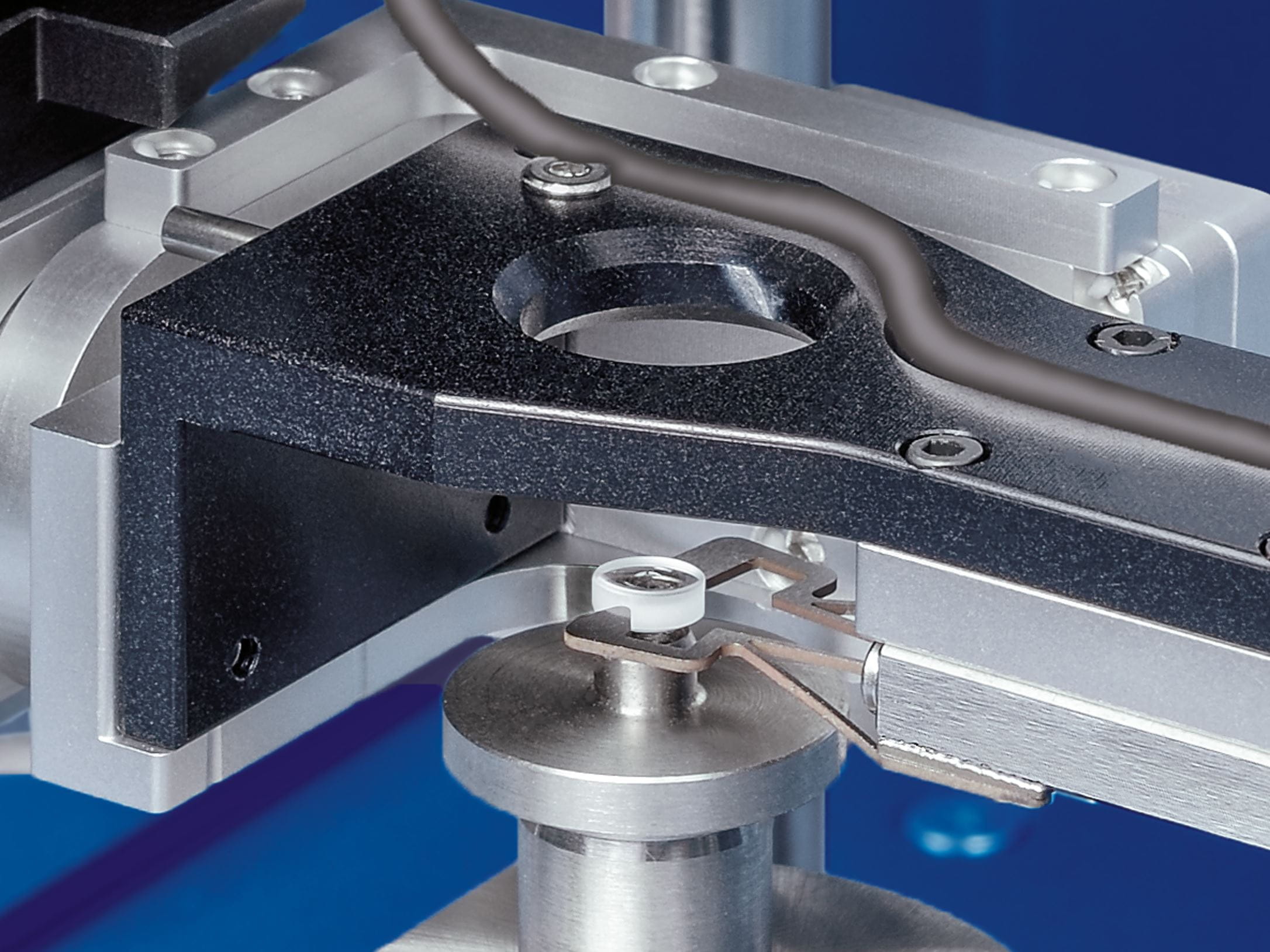
Richtkitten von Linsen auf Zentrierdorn
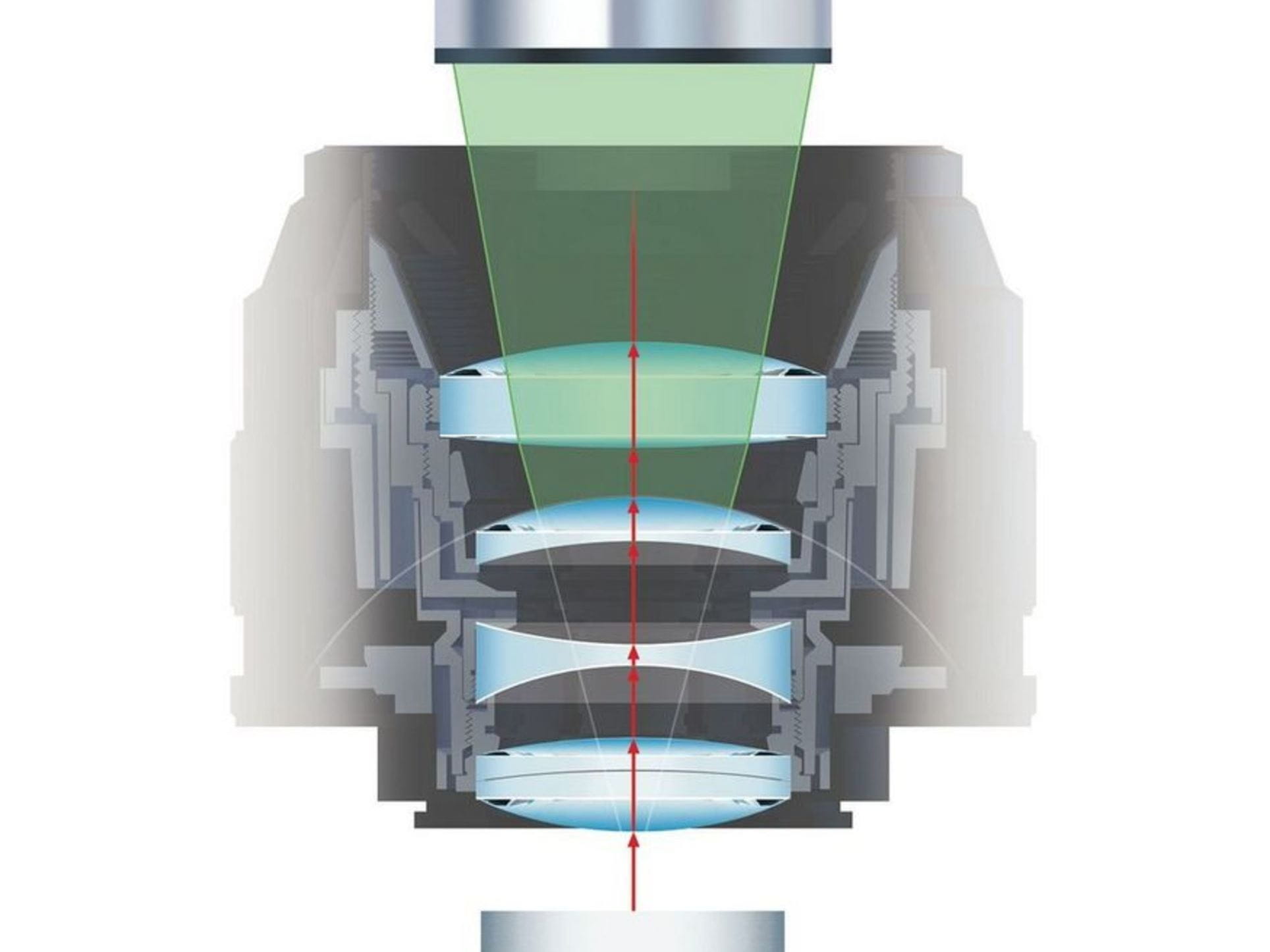
Mittendicken- und Luftabstandsmessung in Kombination mit der Zentrierprüfung von Optiken
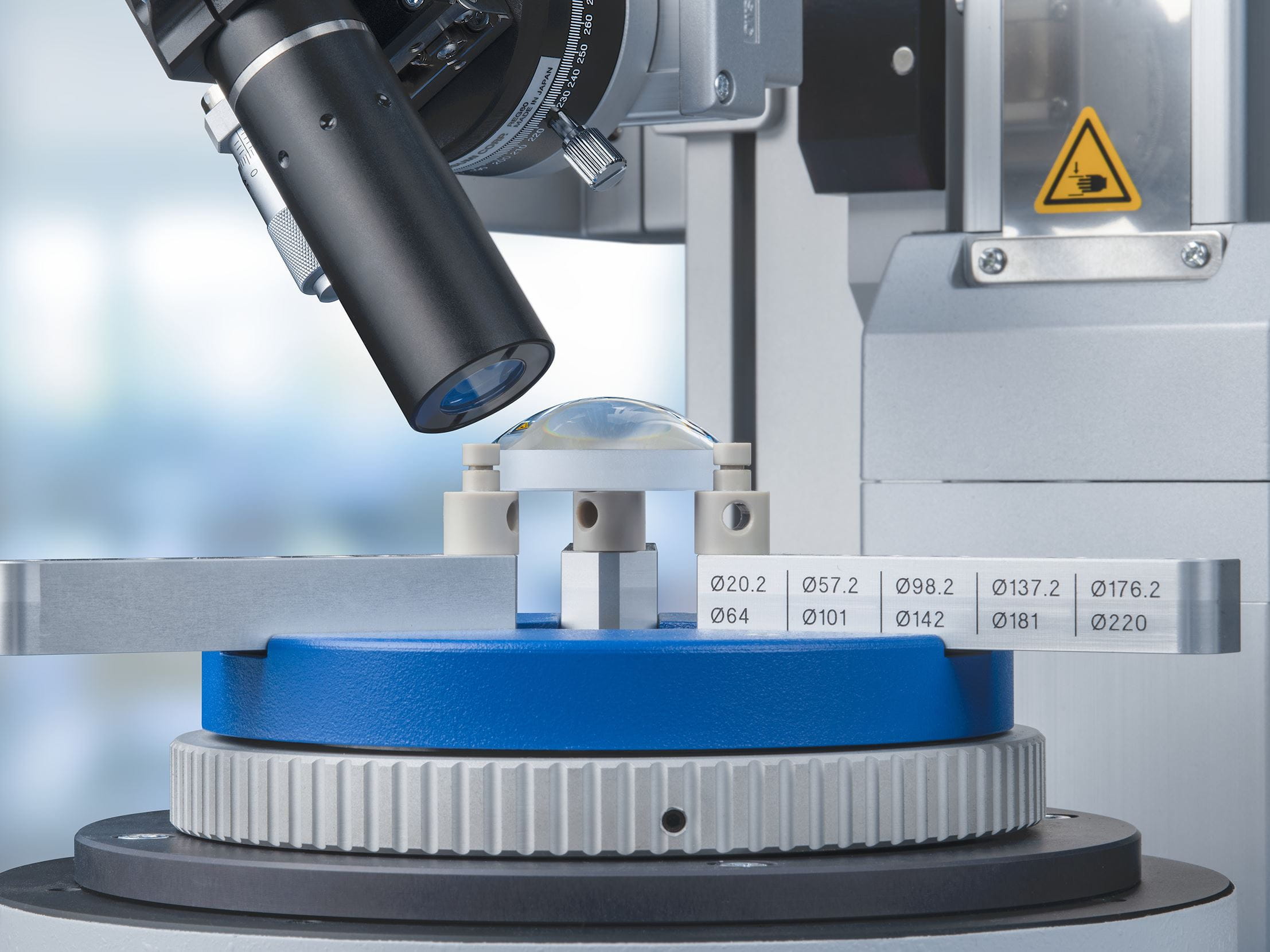
Prüfung von Asphären
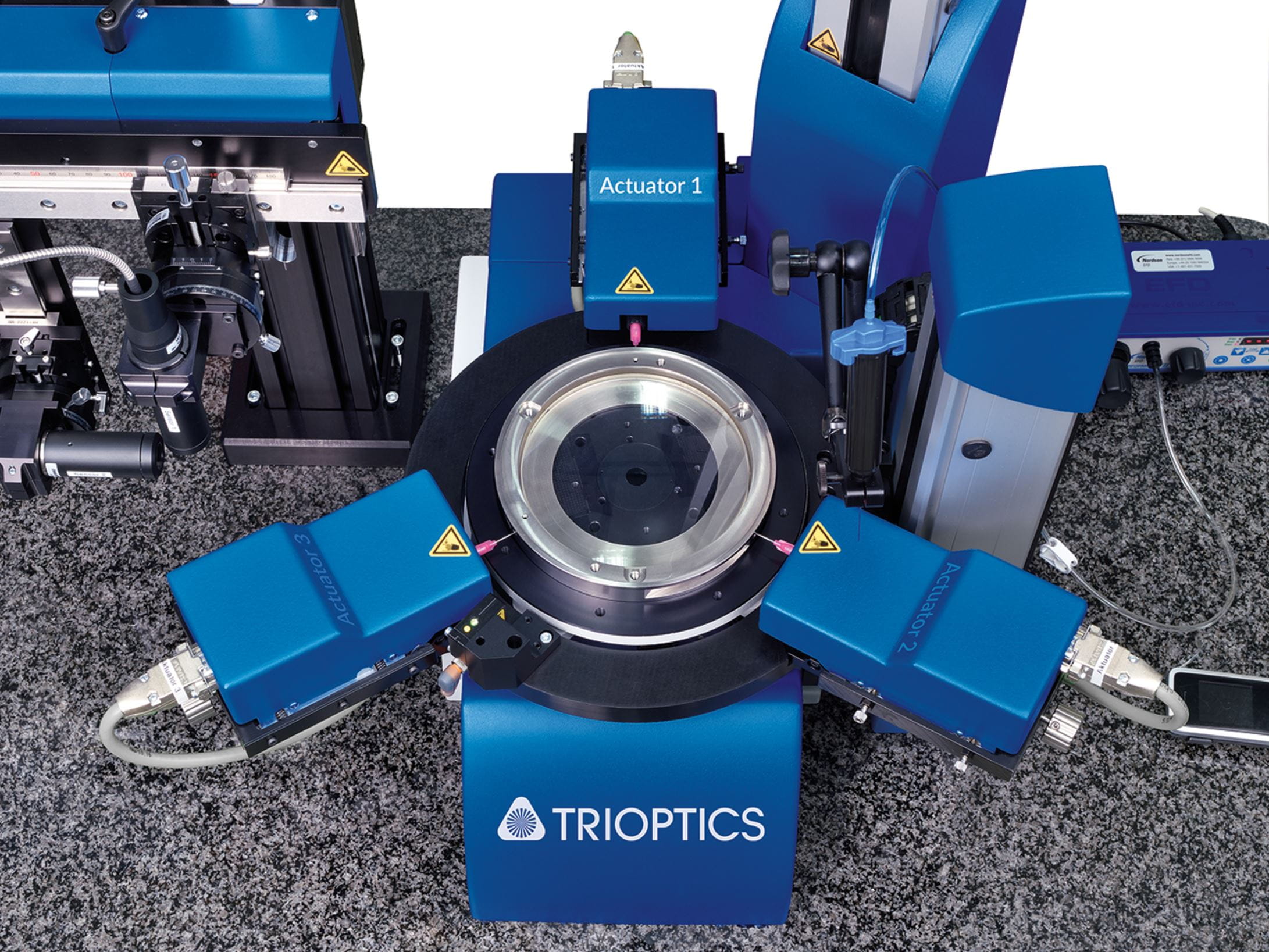
Richtkleben in zwei Freiheitgraden
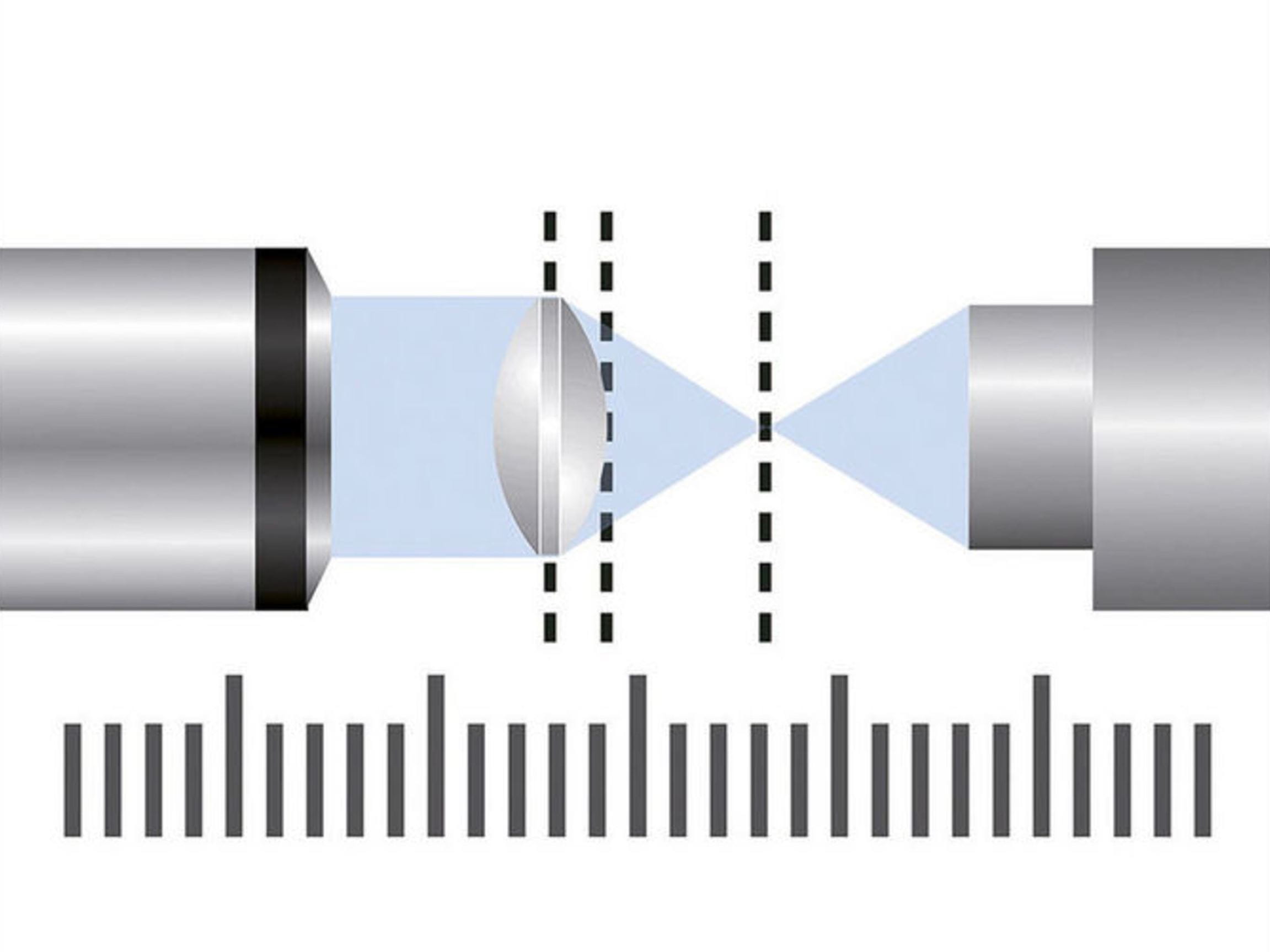
Zentrierfehler, Brennweiten, Anlagemaß, Radius und MTF auf der Achse zusätzlich zur Zentrierprüfung
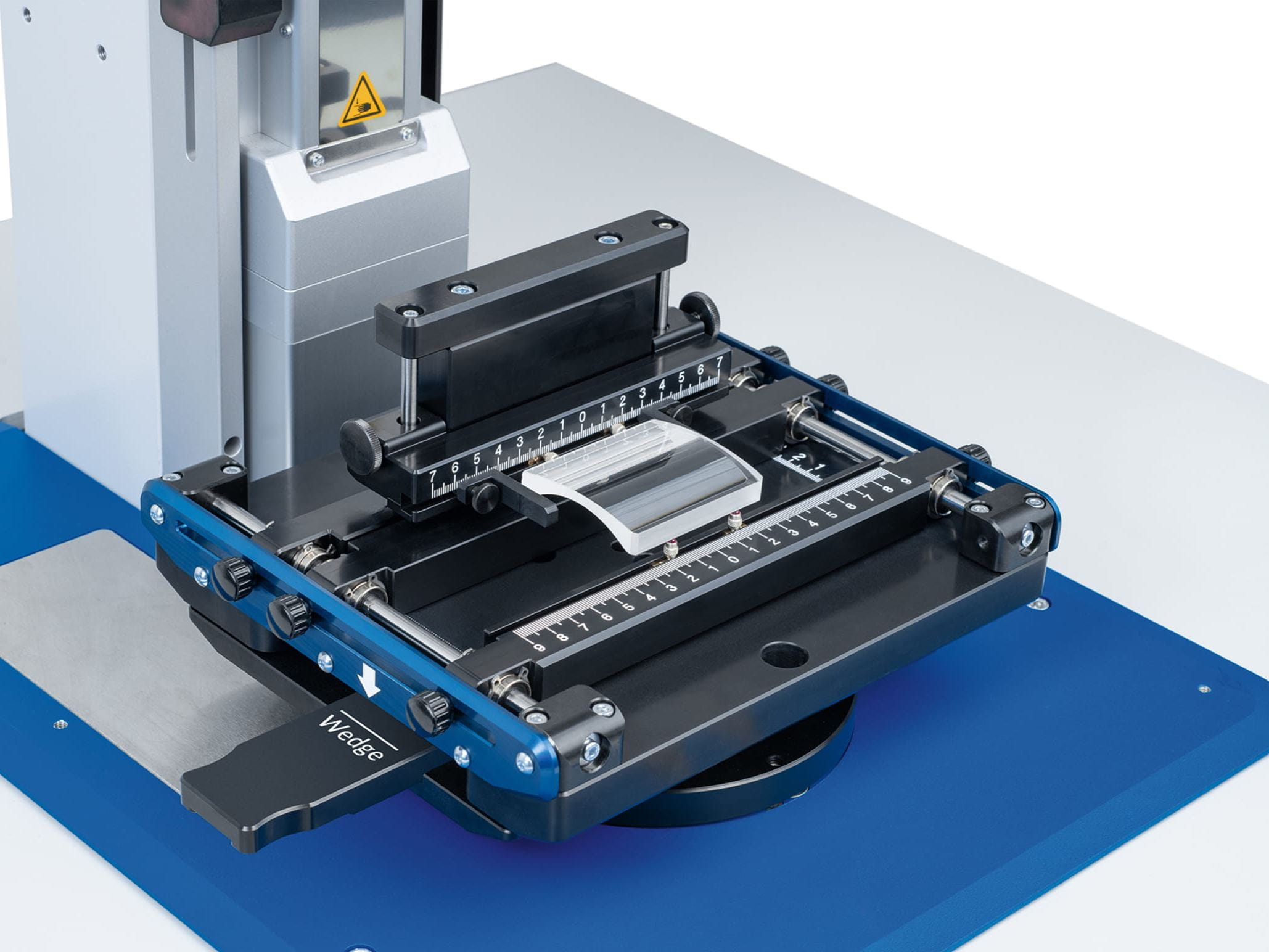
Prüfung von Zylinderlinsen
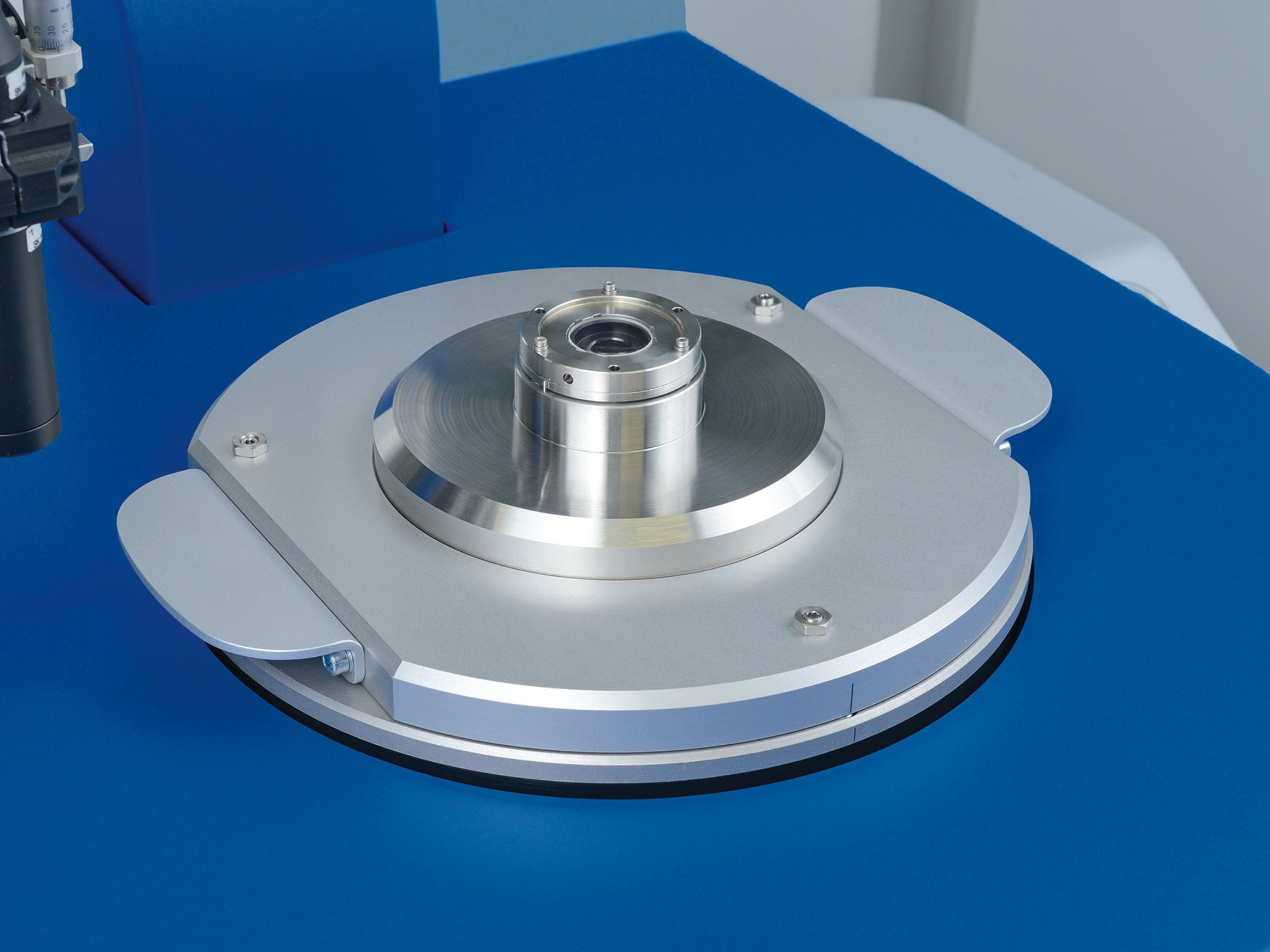
Richtkleben in fünf Freiheitgraden
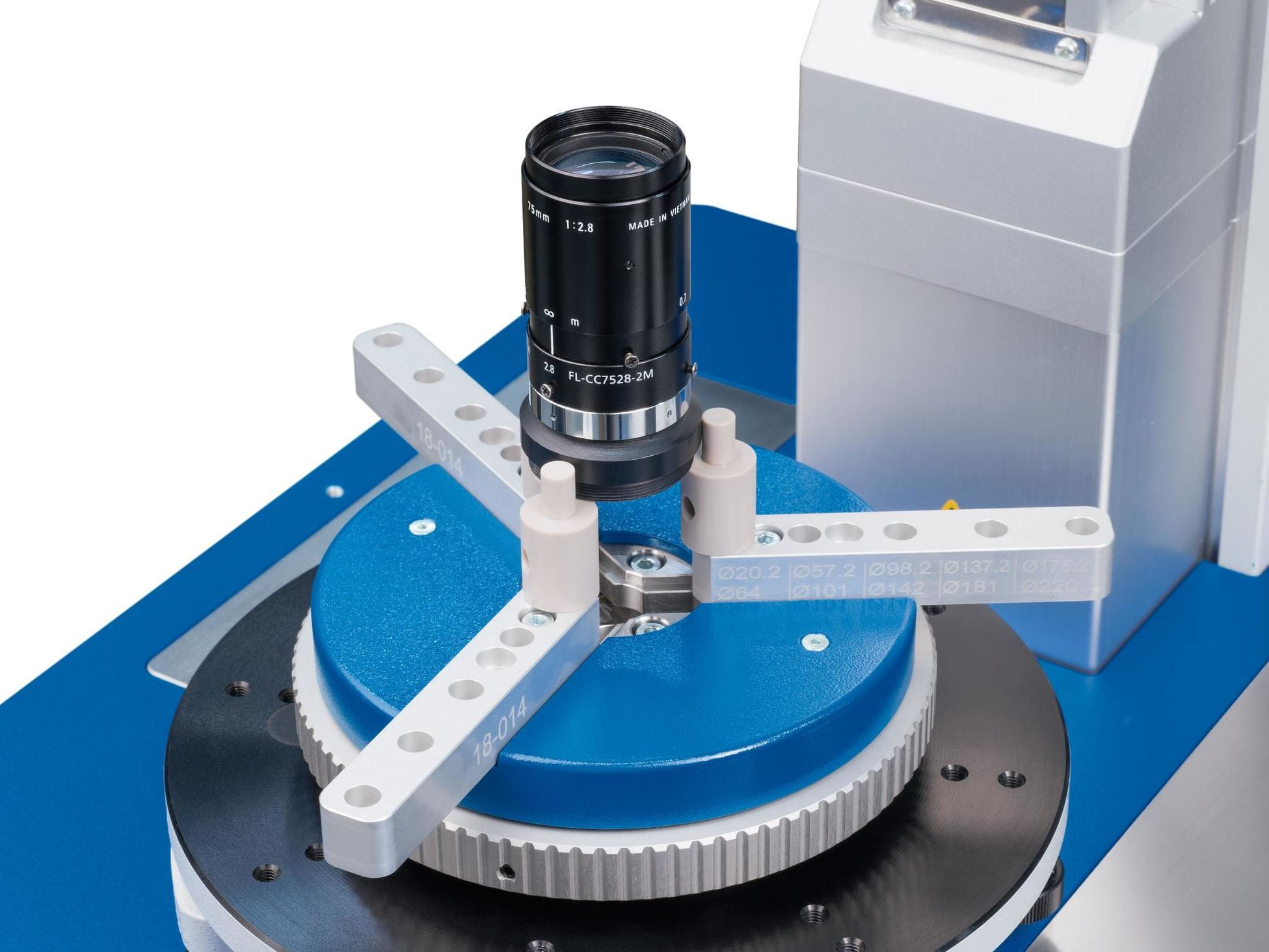
Zentrierprüfung von Gruppen von Flächen innerhalb von optischen Systemen
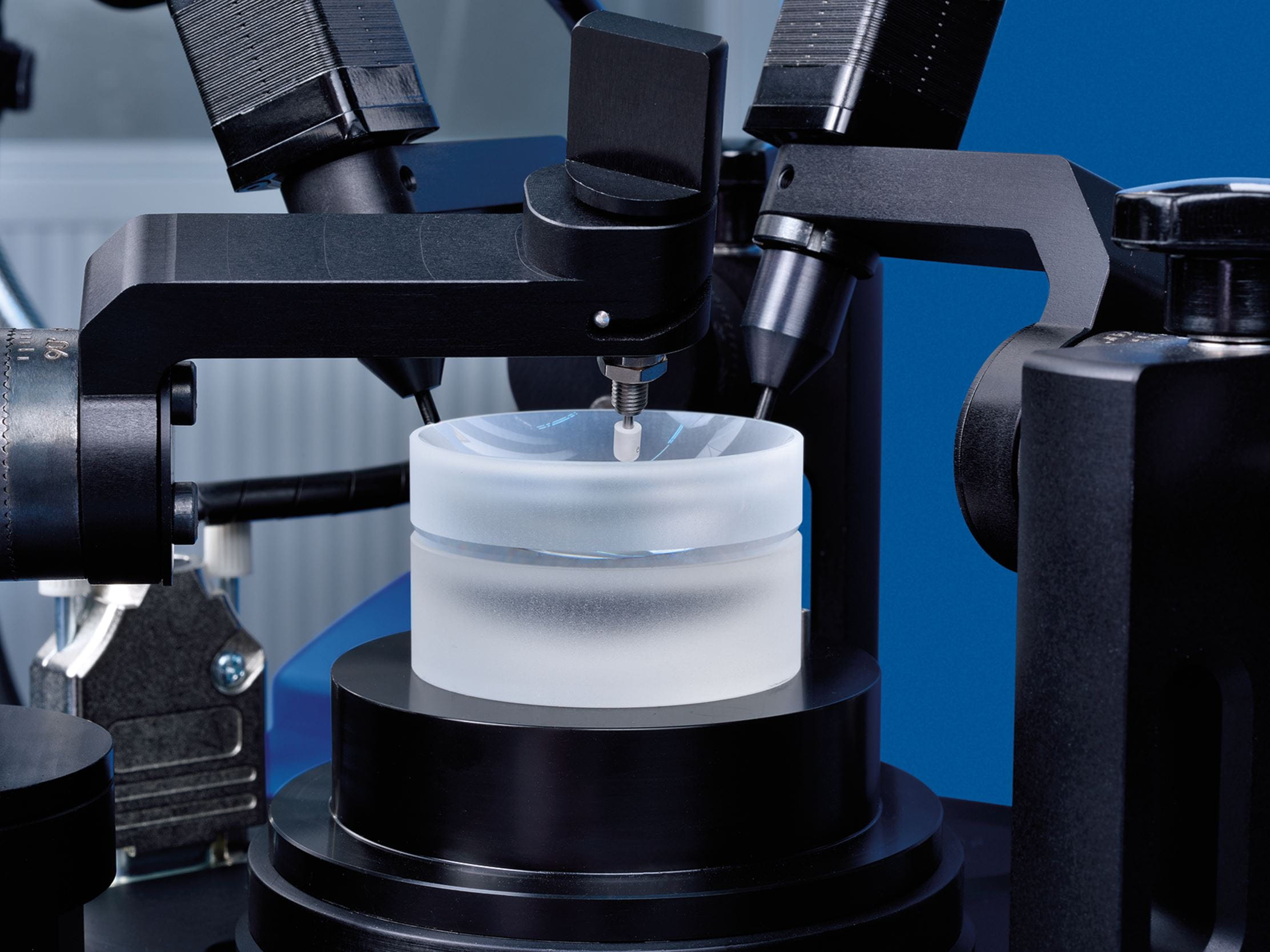
Feinkitten von Achromaten
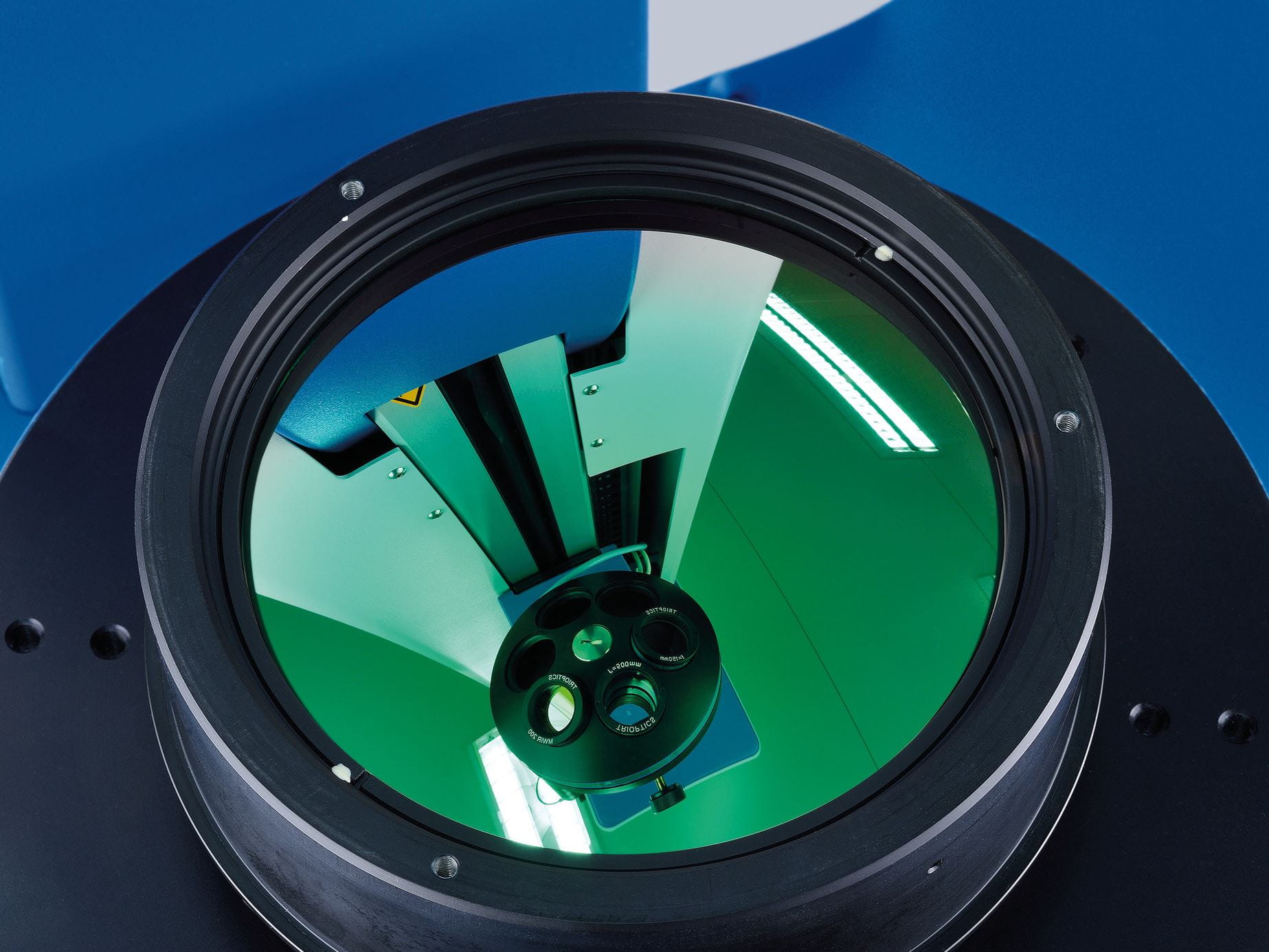
Zentrierprüfung von Flächengruppen innerhalb von Infrarot-Objektiven
Coffee Break
Keine Zeit für lange Erklärvideos?
Wir fassen für Sie ein Thema kurz und prägnant zusammen. Während einer Kaffeepause erhalten Sie die Kernaussagen zu den unterschiedlichsten Technologiethemen.
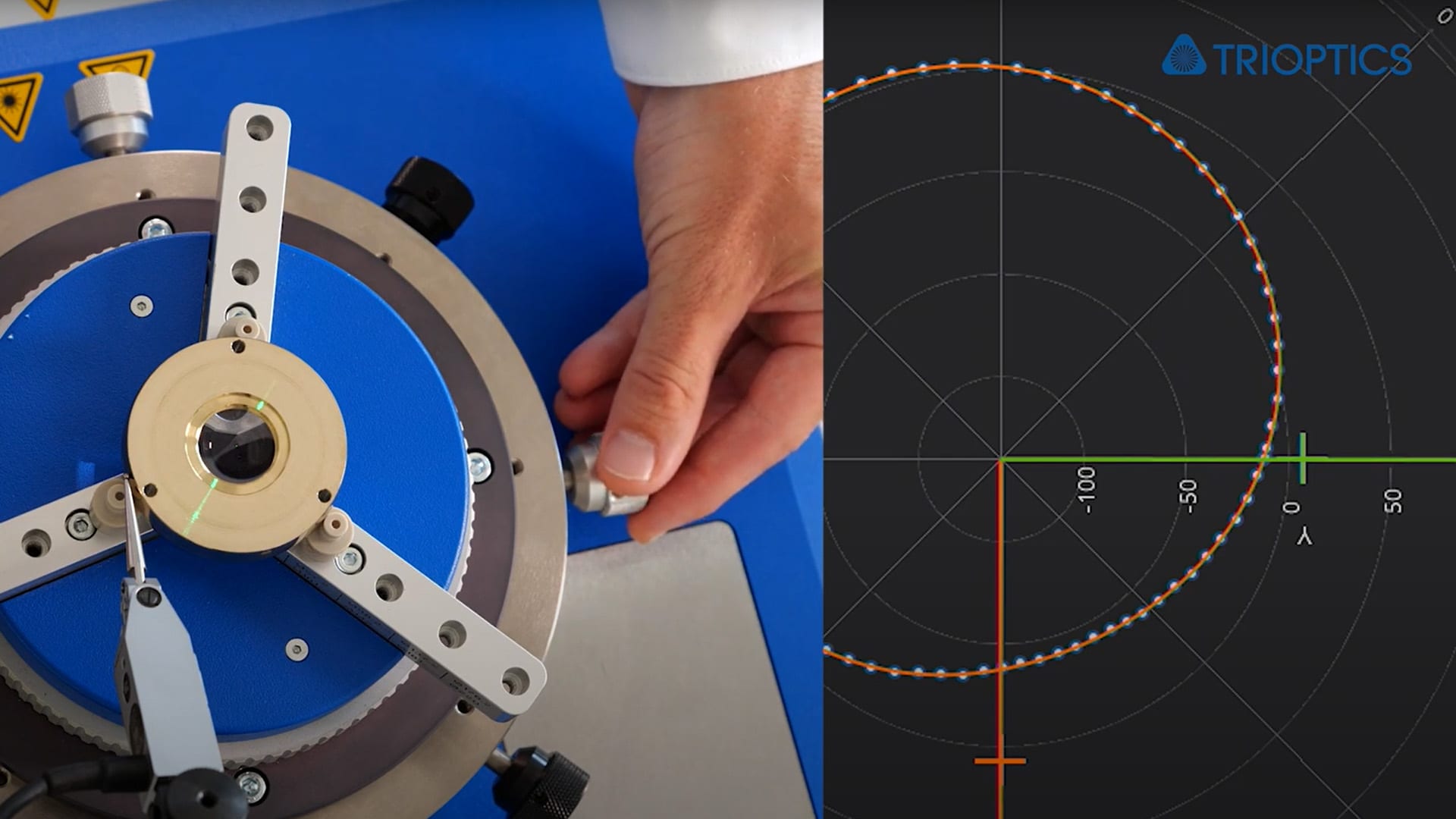
Manuelle Fassungsausrichtung
Fassungsausrichtung auf einem Kipp- und Verschiebtisch mit Polardarstellung
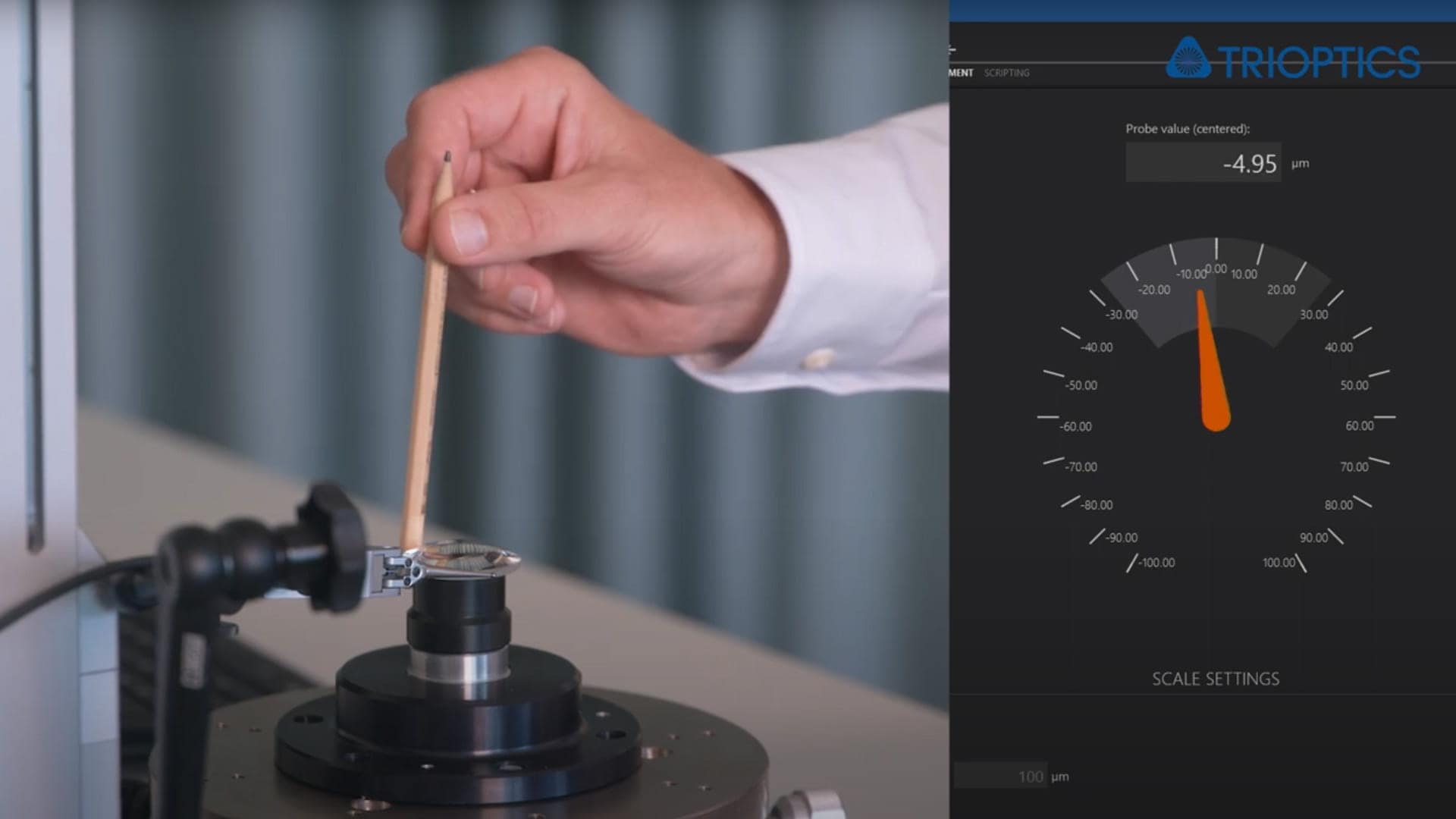
Skaliert und zentriert
Manuelle Linsenausrichtung leicht gemacht
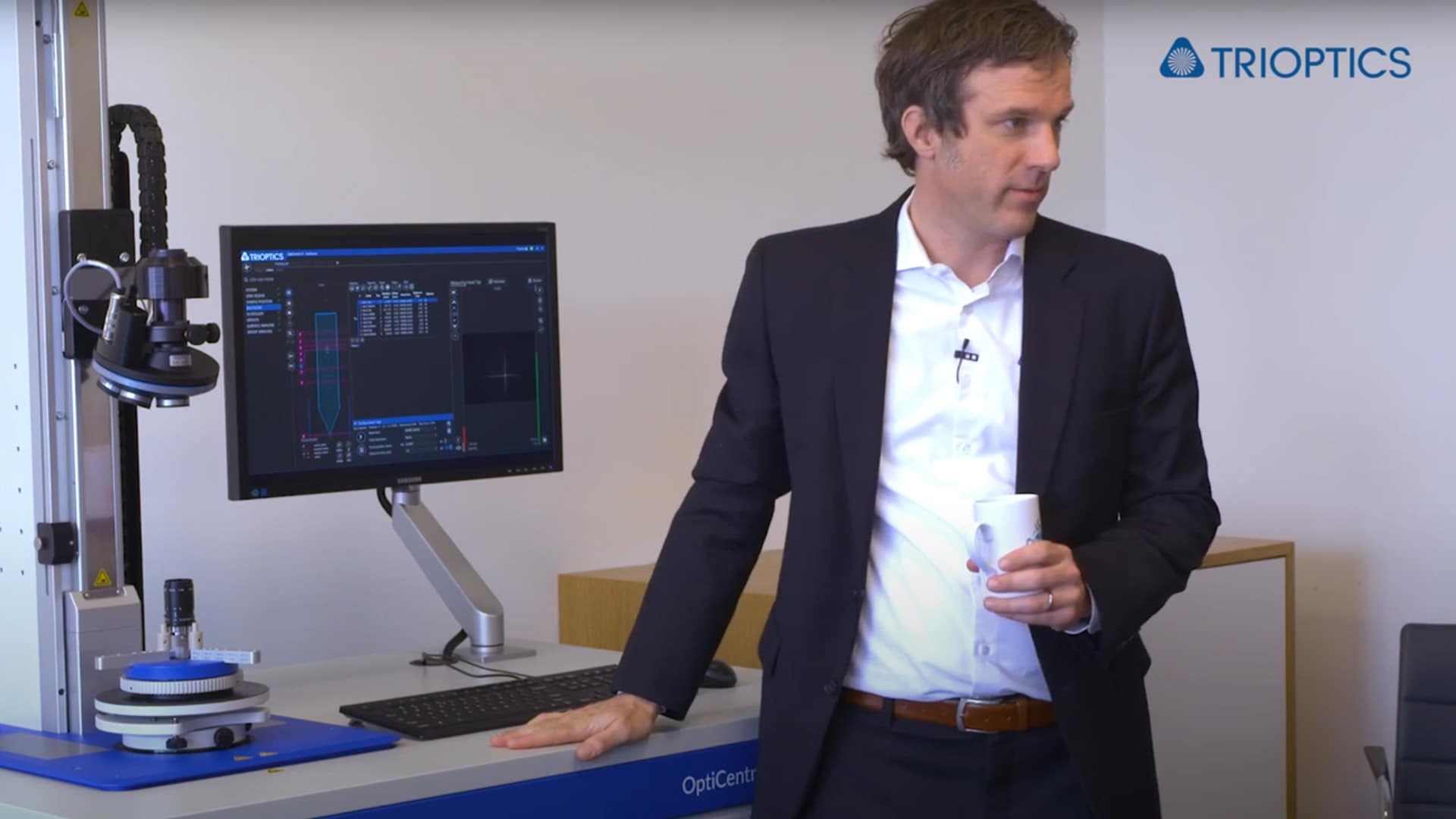
Vom Wechsel profitieren
Effiziente Zentrierprüfung durch Wechsel der Vorsatzoptik
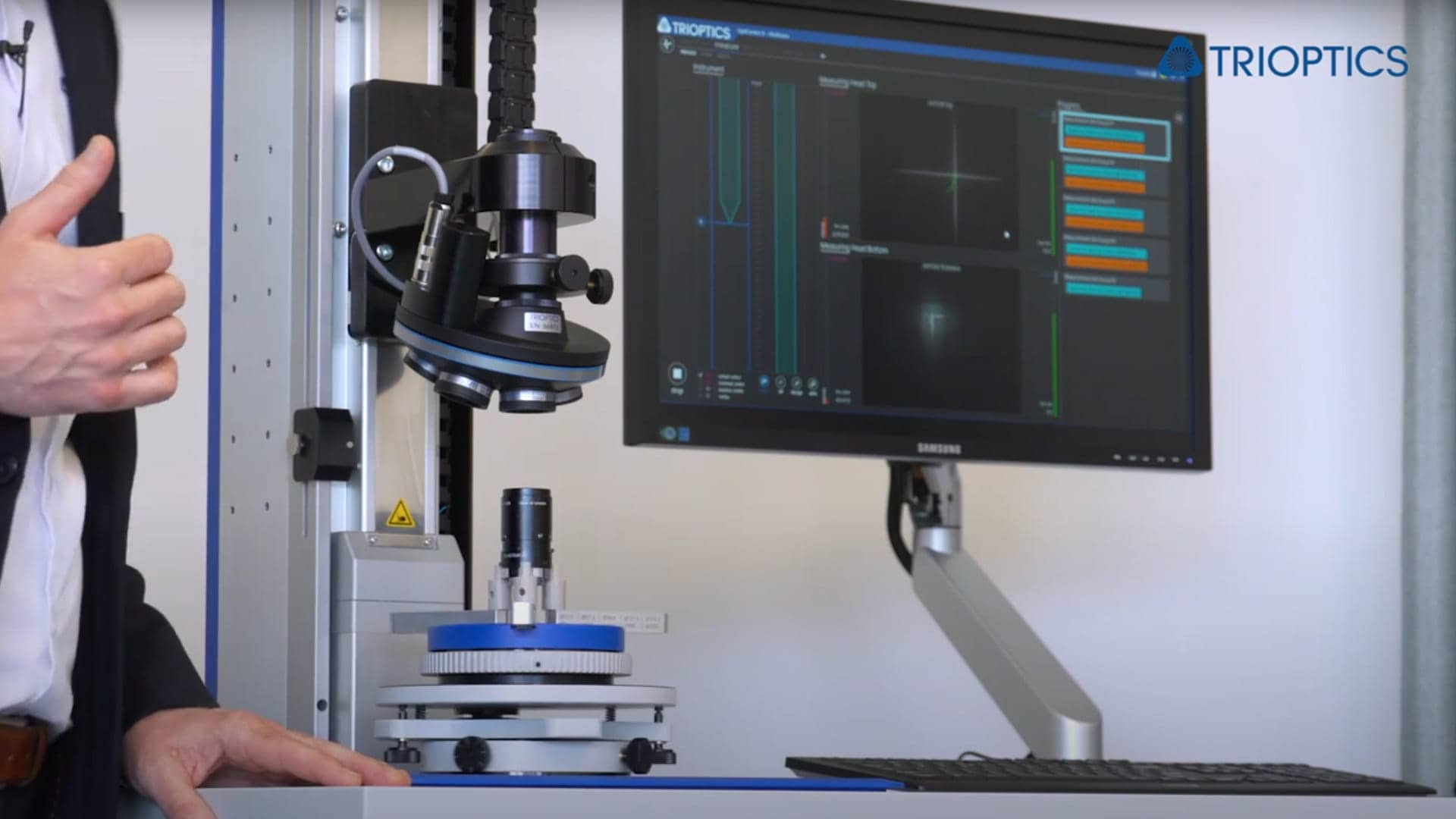
Komplexe Objektive einfach schneller messen
OptiCentric® 101 mit dualem Messkopf
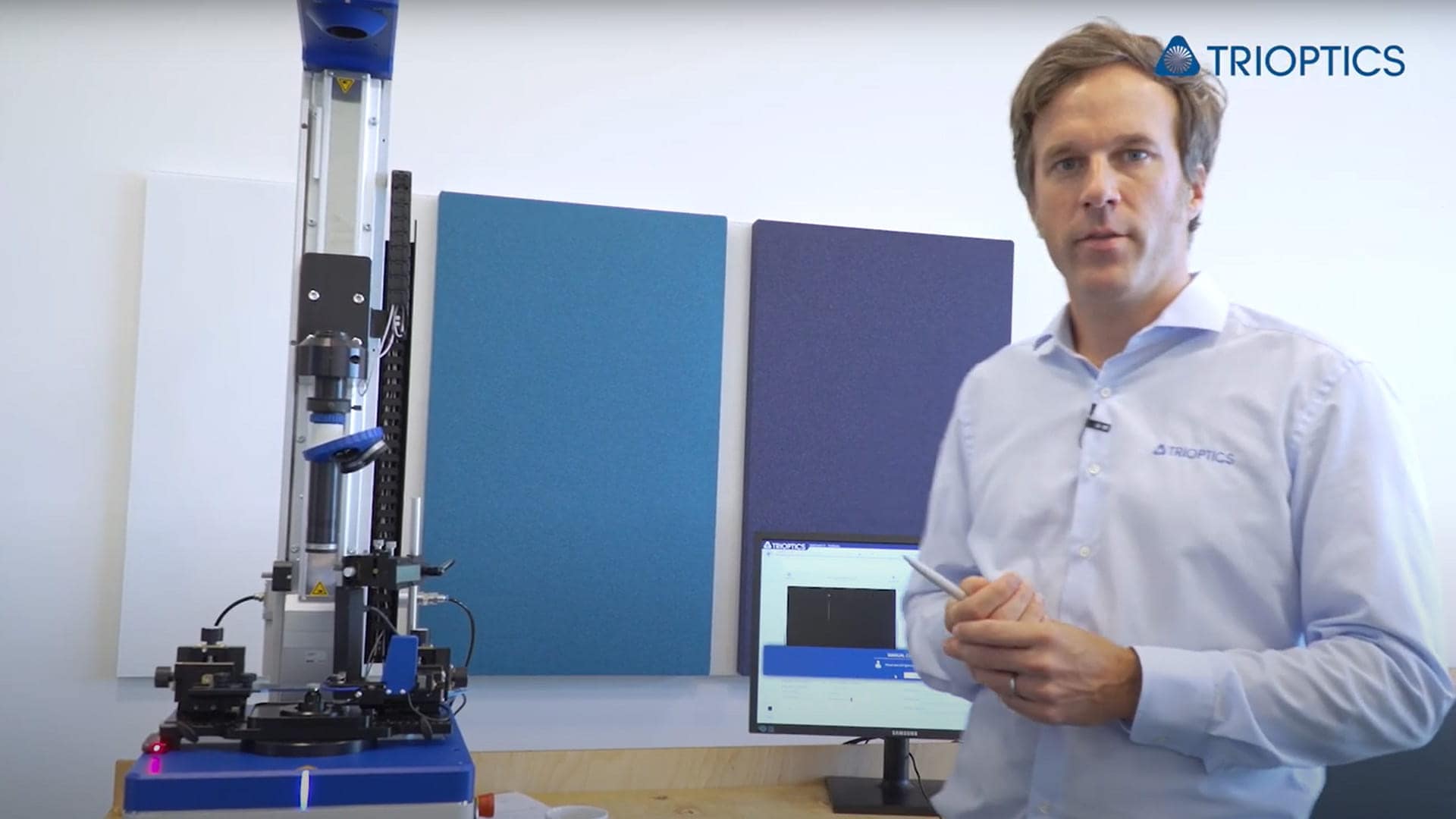
Mehr als heiße Luft
OptiCentric® mit LensAlign 2D Air
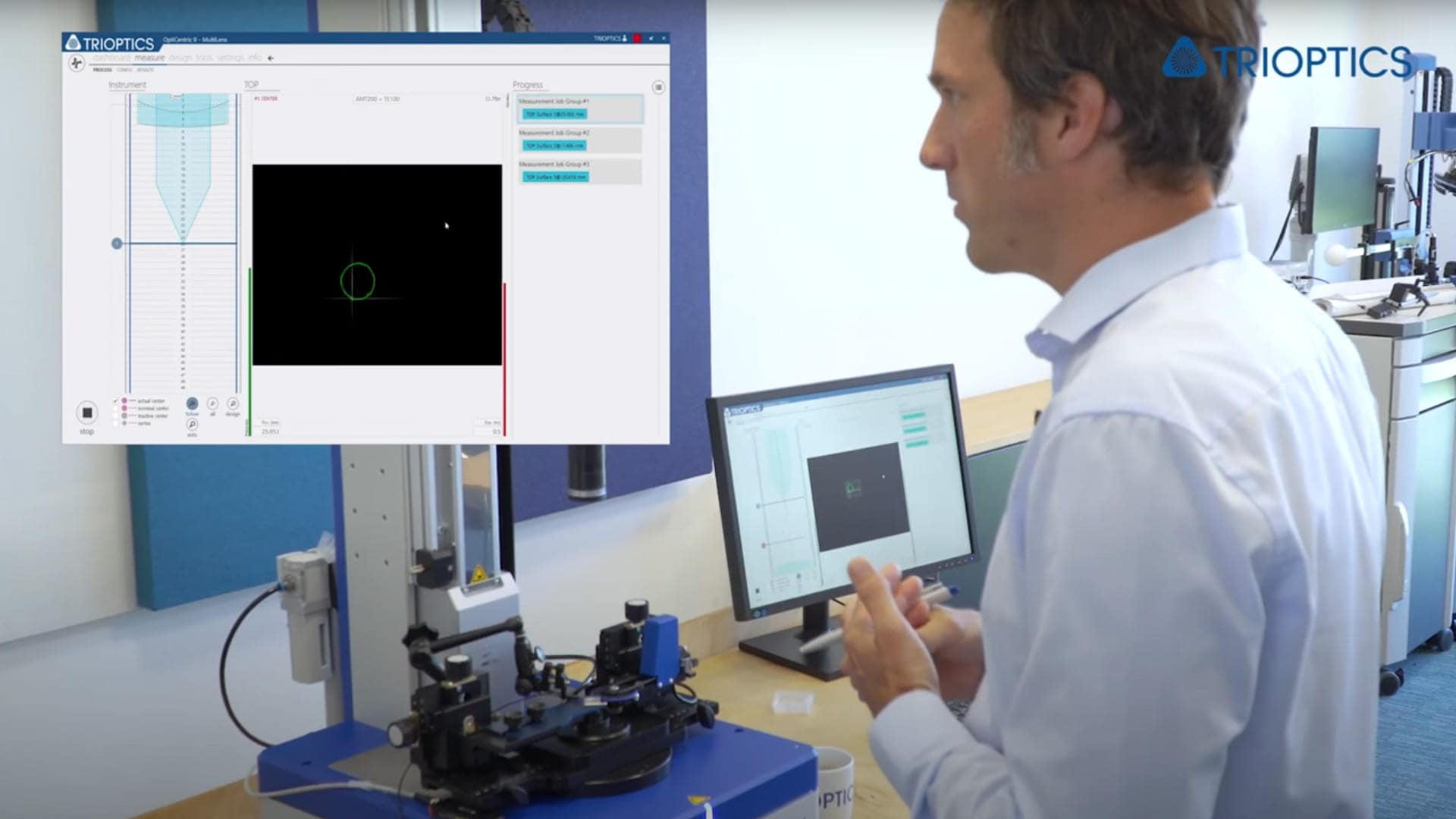
Drehvorrichtung mit System
Zentrierprüfung von Linsensystemen zum Rand
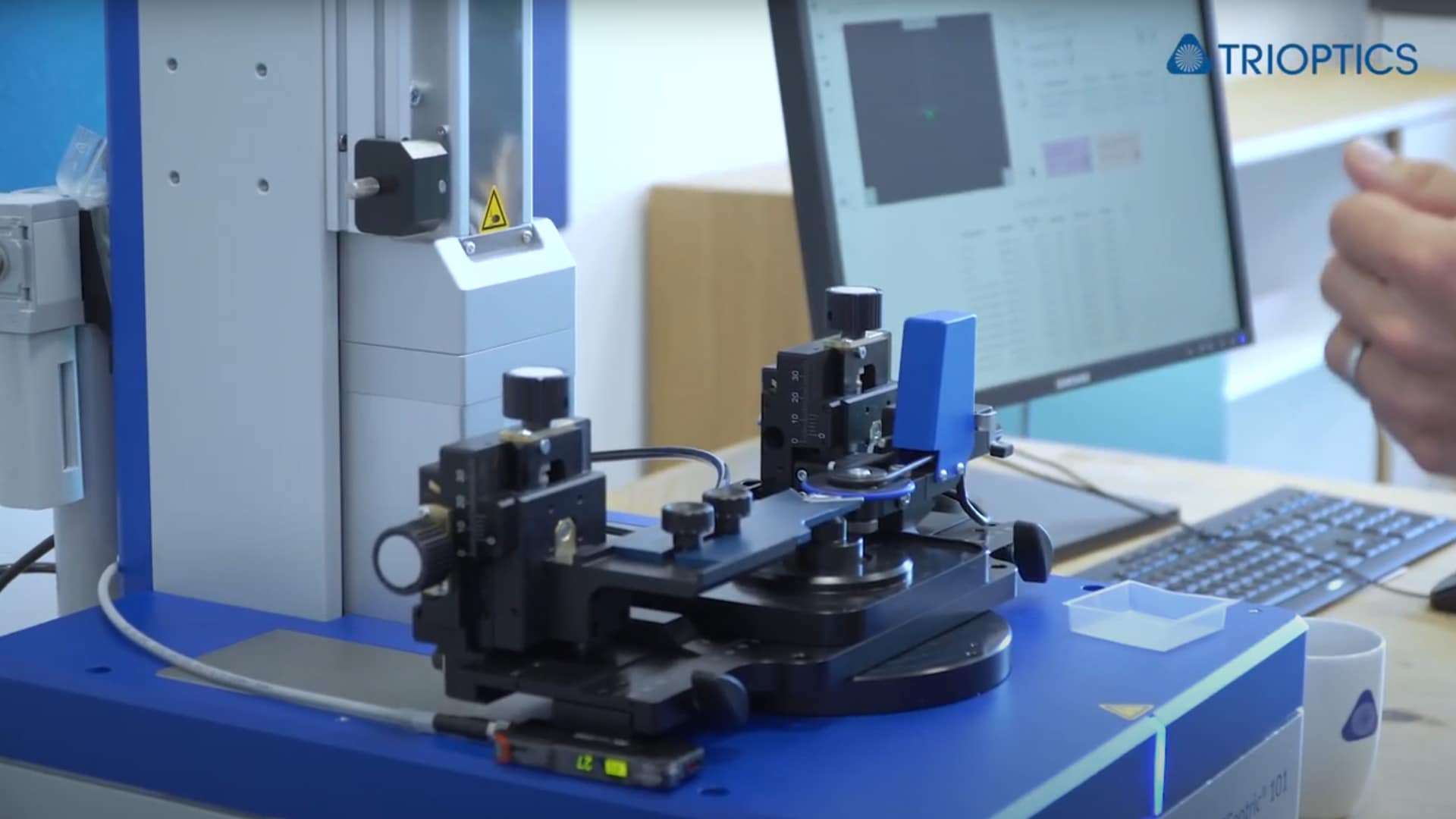
Der Dreh zur Effizienzsteigerung
Neue Linsendrehvorrichtung für OptiCentric®
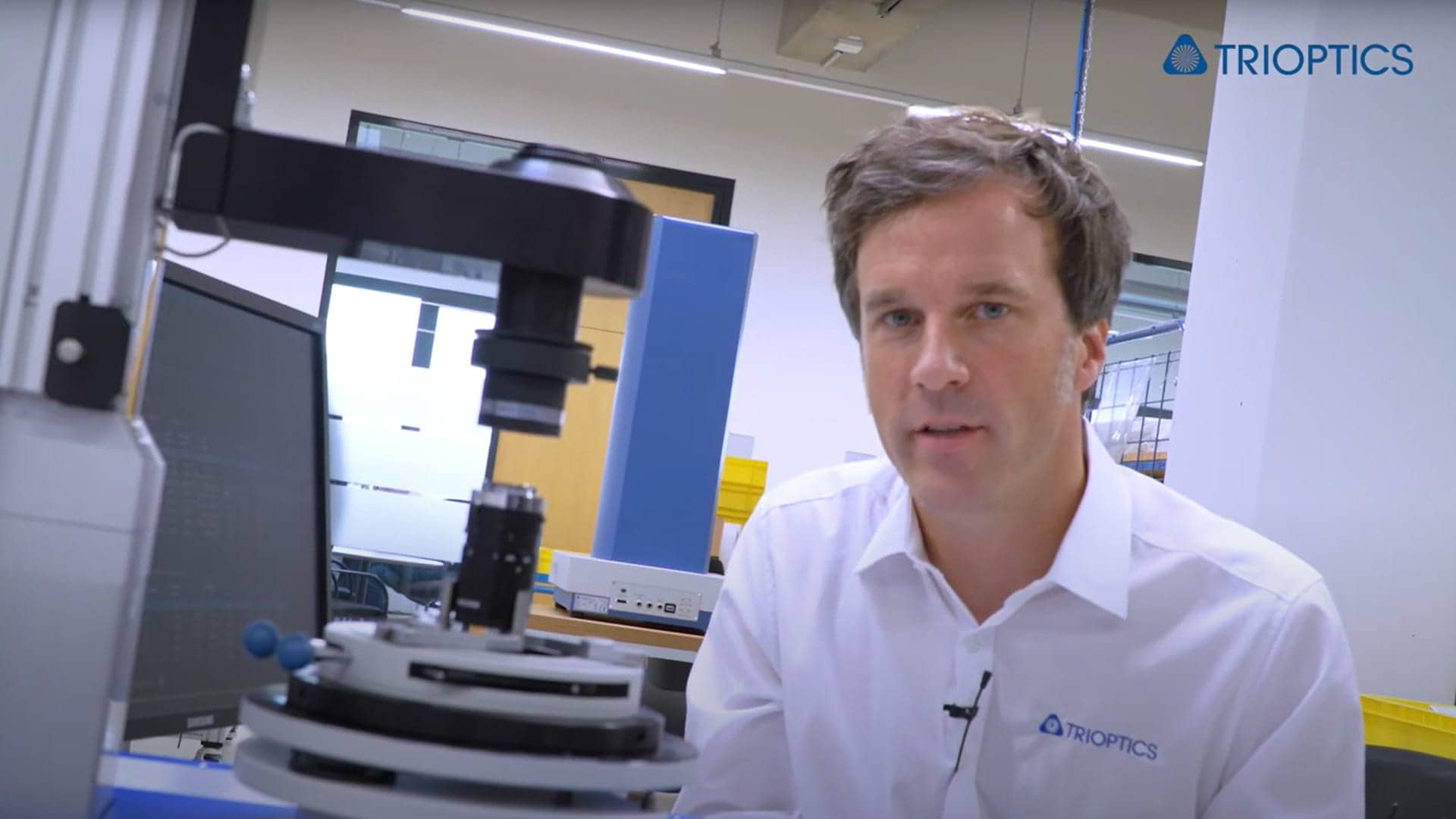
Schnell, schneller, linear
OptiCentric® im linearen Messmodus
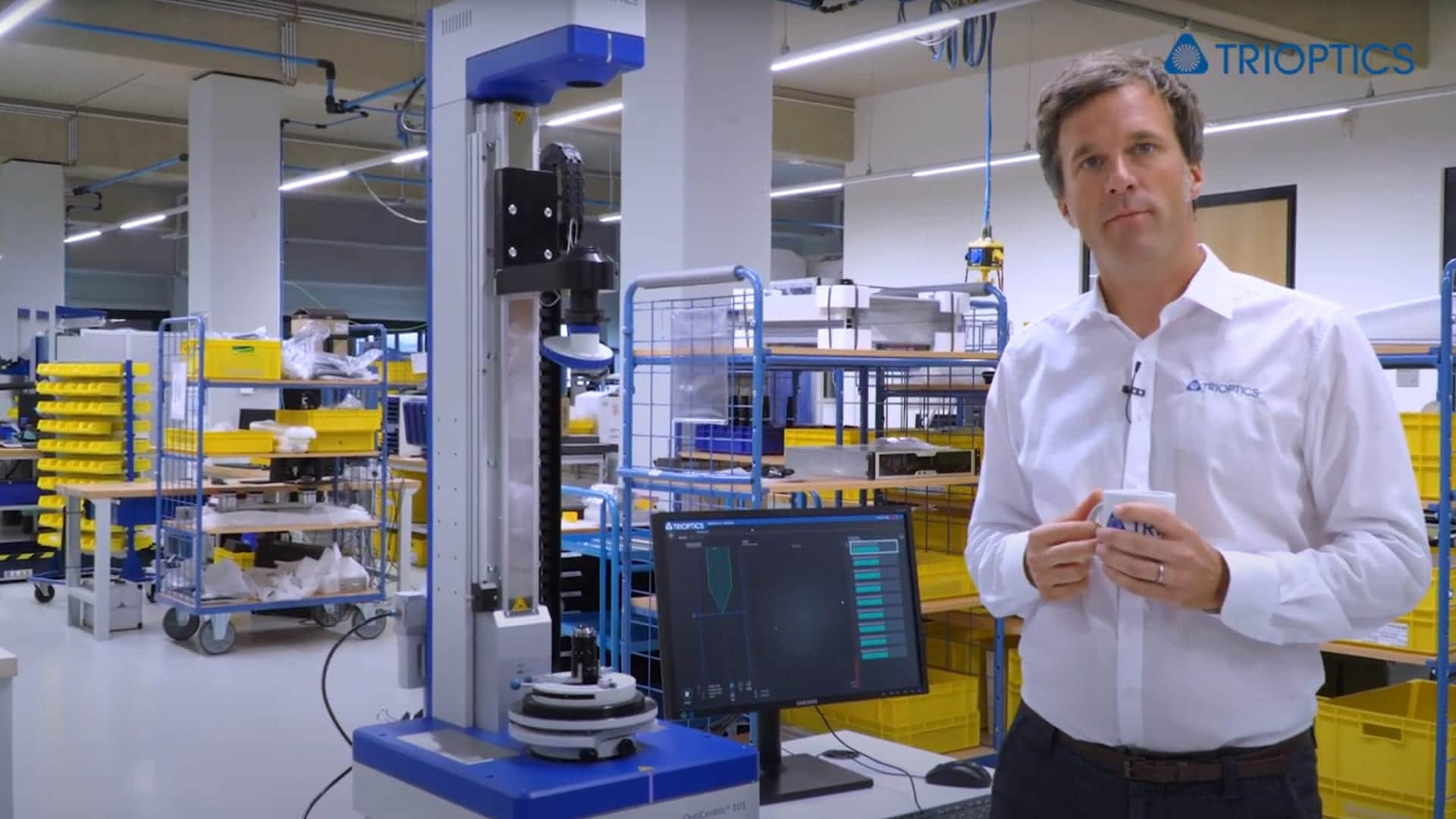
Statisch als neuer Maßstab
OptiCentric® 101 mit statischem Autokollimator
Sie sind begeistert von der Qualitätssteigerung, die durch das Richtkleben erzielt wird, Verwenden jedoch keinen UV-Kleber oder haben den Klebstoffschrupf als kritischen Faktor zur Erreichung ihrer Qualitätsanforderungen ausgemacht? Dann schauen Sie sich doch einmal unsere Justierdrehmaschinen an!
Knowledge base
- Zentrierfehler messen, Linsen ausrichten, verkitten und kleben
- Prinzip der Zentrierfehlerprüfung in Reflexion und Transmission
- Die Zentrierfehlermessung
- Die Ausrichtung
Zentrierfehler messen, Linsen ausrichten, verkitten und kleben
Die präzise Zentrierung und Ausrichtung einer Linse ist ausschlaggebend für die Bildqualität des optischen Systems. Eine fehlerhafte Zentrierung liegt dann vor, wenn die optische Achse der Linse mit der Bezugsachse in Lage und Richtung nicht übereinstimmt (ISO 10110). Zentrierfehler entstehen beim Verkitten, Justieren und Befestigen von Linsen, daher können die hohen Anforderungen an optische Systeme dann am besten erfüllt werden, wenn alle fertigungstechnischen Schritte einheitlich konzipiert und in einem Mess- und Fertigungssystem integriert sind.
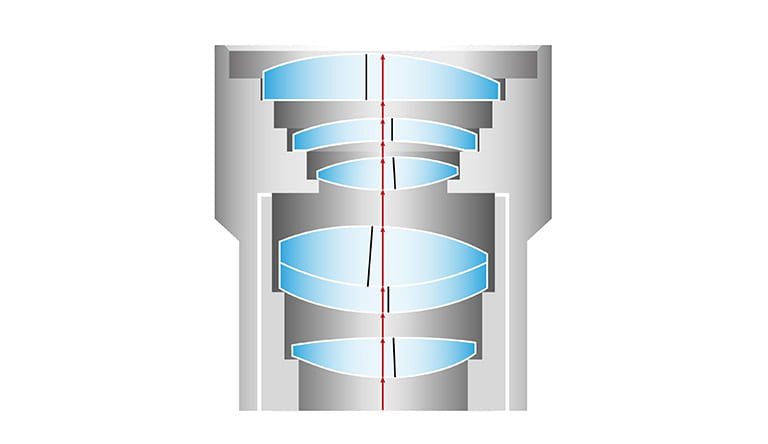
Zentrierfehler von Linsen und Objektiven
Zentrierfehler haben einen entscheidenden Einfluss auf die Abbildungsleistung eines optischen Systems. Ein Zentrierfehler liegt vor, wenn die Symmetrieachse eines optischen Elements nicht mi einer gegebenen Referenzachse übereinstimmt. Die Referenzachse eines Objektivs kann beispielsweise durch die Symmetrieachse des Gehäuses gegeben sein. Der Zentrierfehler wird durch einen Winkel zwischen der optischen Achse und der Referenzachse und dem Abstand eines Symmetriepunkts zur Referenzachse beschrieben.
Eine Übersicht möglicher Zentrierfehler kann der obenstehenden Zeichnung entnommen werden.
- Verschiebung einer Linse
- Kippung einer Linse
- Flächenkippfehler einer sphärischen Oberfläche
- Verschiebung und Kippung einer Linse
- Neigung der Asphärenachse
- Luftabstände und Mittendicken
Das OptiCentric®-System ist in der Lage jeden dieser Fehler präzise und in Übereinstimmung mit der DIN/ISO-Norm 10110-6 zu bestimmen.
Prinzip der Zentrierfehlerprüfung in Reflexion und Transmission
Voraussetzung, um die Zentrierung einer Linse zu messen, ist, dass die Linse um eine präzise Referenzachse rotiert. Diese Achse entspricht in den meisten Fällen der Rotationsachse eines Drehlagers. Sie ist maßgebend für die präzise Messung der Zentrierung. Darüber hinaus kann die Zentrierung einer Linse auf zwei unterschiedliche Arten gemessen werden. Es wird zwischen der Messung in Reflexion und Transmission unterschieden.
Zentriermessung in Reflexion
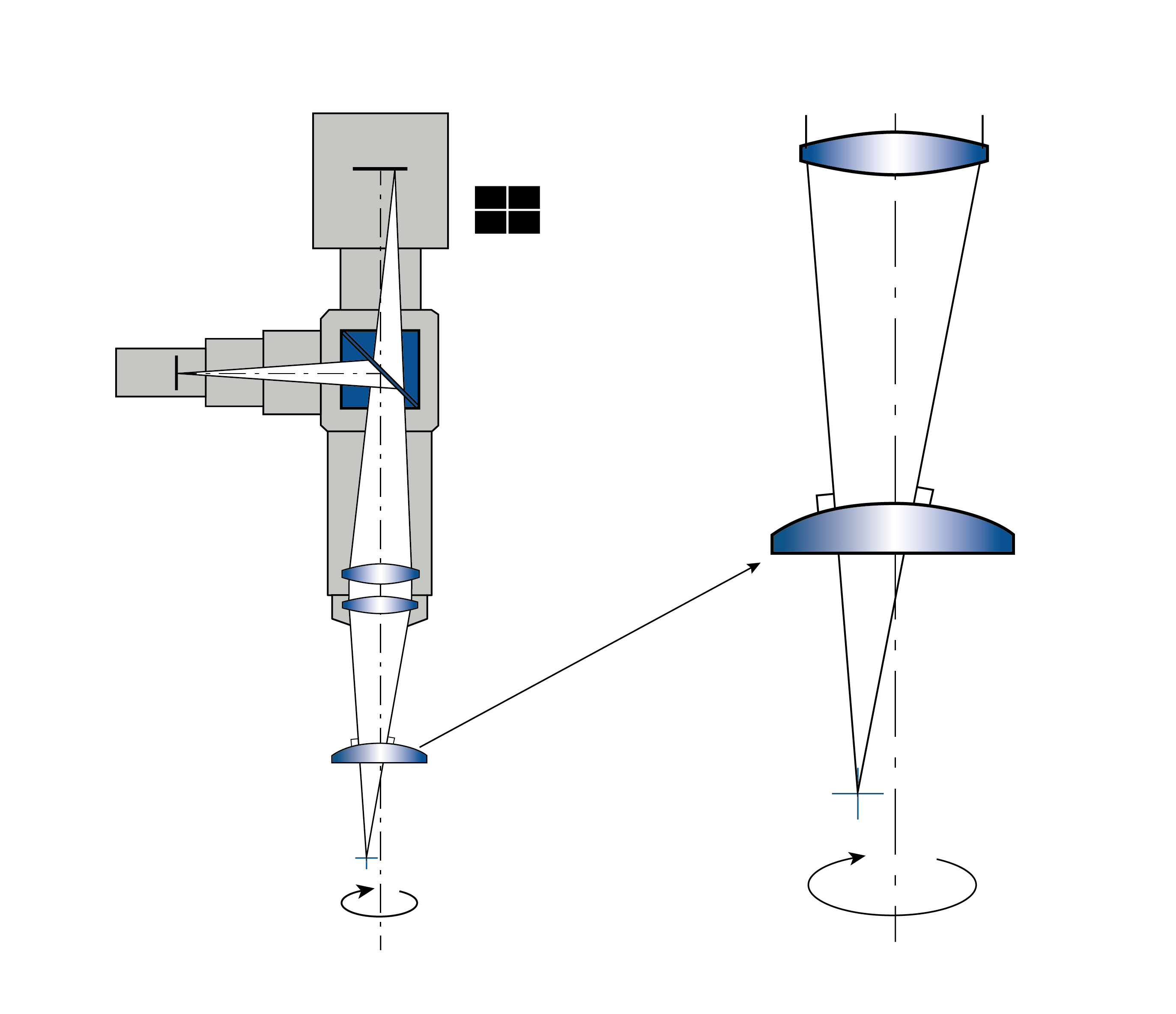
Zentriermessung in Reflexion
Für die Messung in Reflexion wird ein OptiCentric®-System verwendet. Es ist mit einem Autokollimationsmesskopf mit Strichplatte und entsprechender Vorsatzoptik ausgestattet. Für die Messung wird der Messkopf mit der Vorsatzoptik auf den Krümmungsmittelpunkt der zu untersuchenden Linsenfläche fokussiert. Das erzeugte Reflexbild der Strichplatte wird mit Hilfe der in den Messkopf integrieren Kamera beobachtet und mit der Software ausgewertet.Liegt ein Zentrierfehler vor, so beschreibt das betrachtete Bild einen Kreis, während der Prüfling um die Referenzachse rotiert. Der Mittelpunkt des beschriebenen Kreises liegt auf der Referenzachse. Der Radius des Kreises ist proportional zum Zentrierfehler und beschreibt den Abstand des Krümmungsmittelpunkts der Linsenoberfläche zur Referenzachse. Soll der Zentrierfehler als Winkel beschrieben werden, so spricht man bei der Messung in Reflexion vom Flächenkippfehler. (Siehe auch ISO 10110).
Zentriermessung in Transmission
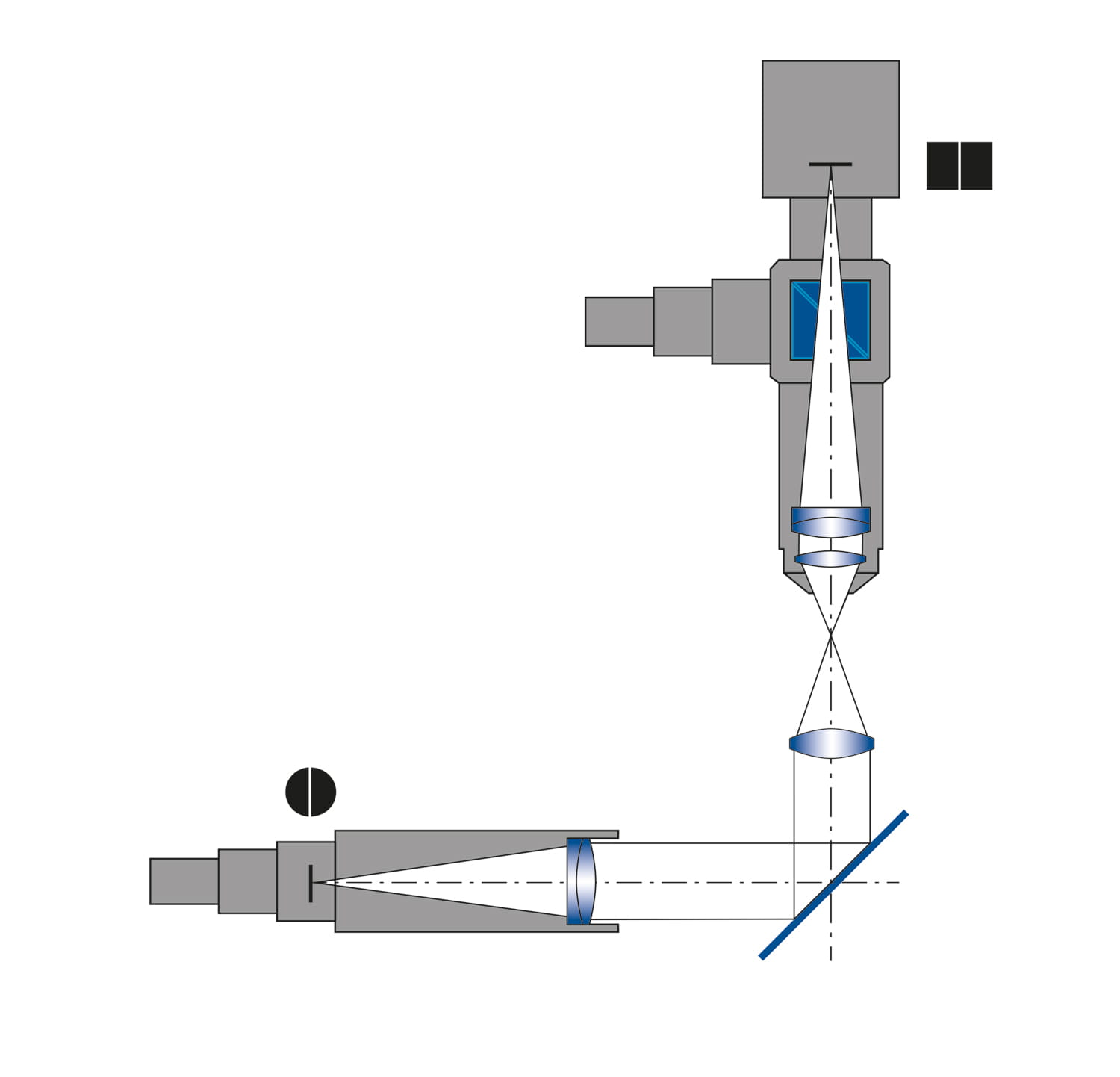
Zentriermessung in Transmission
Bei der Transmissionsmessung ist das OptiCentric®-System ebenfalls mit dem Autokollimationsmesskopf und entsprechender Vorsatzoptik ausgestattet. Zusätzlich muss das System für die Transmissionsmessung mit einem Kollimator mit Strichplatte im Fuß des Messsystems versehen werden.Bei der Transmissionsmessung erzeugt das parallele Licht des Kollimators ein Bild der Strichplatte in der Fokusebene des Prüflings, in die auch die Vorsatzoptik des Autokollimationskopfes fokussiert. Mit Hilfe der Kamera kann das Bild nun ausgewertet werden. Liegt ein Zentrierfehler vor, beschreibt das Bild wie bei der Messung in Reflexion einen Kreis.
Der Radius des Kreises entspricht dem Abstand zwischen der Referenzachse und dem Fokuspunkt. Als Winkel kann der Zentrierfehler bei der Messung in Transmission als Neigung des Hauptstrahls angegeben werden.
Zentriermessung in Reflexion versus Zentriermessung in Transmission
Zentriermessung in Reflexion versus Zentriermessung in Transmission
Die Reflexions- und Transmissionswerte sind unterschiedlich und können nur eingeschränkt verglichen werden. Eine einfache Beziehung zwischen den beiden Messungen für den Zentrierfehler einer Einzellinse (ohne Fassung) ist gegeben durch:T = (n – 1) × R
T: Winkelabweichung in Transmission
n: Brechungsindex von Glas
R: Oberflächenneigungsfehler der Oberseite (Ergebnis der Messung im Reflexionsmodus)
Bei der Transmissionsmethode ist es grundsätzlich nicht möglich zu unterscheiden, welche der Linsenoberflächen mit einem Zentrierfehler behaftet ist. In bestimmten Fällen kann es vorkommen, dass eine in Transmission gemessene Linse keine Zentrierfehler aufweist, obwohl die Linse schräg in der Fassung montiert ist. Die Zentrierfehlermessung in Reflexion liefert klare, geometrisch interpretierbare, Ergebnisse für eine einzelne optische Oberfläche.
Beide Methoden sollten in Betracht gezogen werden, um eine effiziente optische Produktion zu erreichen.
Zentrierfehler von Einzellinsen
Zentrierfehler von Einzellinsen
Die optische Achse einer Einzellinse ist die Gerade durch die Krümmungsmittelpunkte der beiden Sphären. Der Zentrierfehler ist nun durch einen Winkel „χ” und durch einen Abstand „a“ zu einer gegebenen Bezugsachse definiert.Der Zentrierfehler einer Einzellinse kann ebenfalls in Bezug auf die Randbearbeitung dargestellt werden. In diesem Fall wird er als Flächenkippfehler oder Keilfehler der Linse bezeichnet. Als Referenzachse wird eine Gerade durch einen der Krümmungsmittelpunkte und den Mittelpunkt des Linsendurchmessers festgelegt. Ausgegeben wird der Flächenkippfehler der oberen Fläche bezogen auf diese Bezugsachse.
Zentrierfehler von asphärischen Linsen
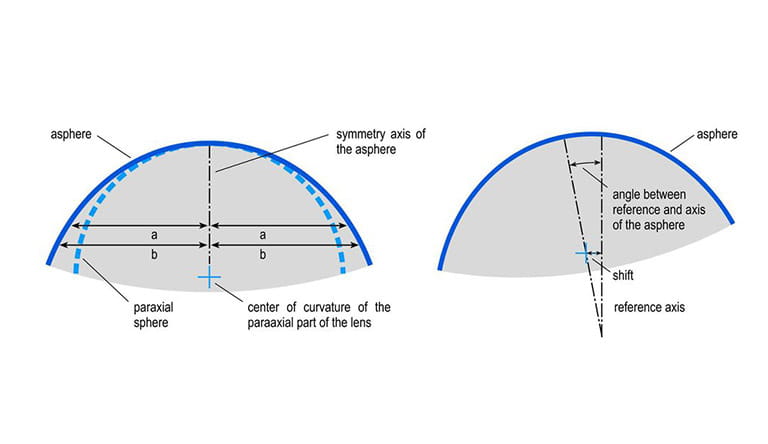
Zentrierfehler von asphärischen Linsen
Im Gegensatz zu sphärischen Oberflächen verfügen rotationssymmetrische asphärische Flächen über eine Symmetrieachse.
Ziel der Zentrierfehlermessung ist daher die Lagebestimmung dieser Symmetrieachse zur Bezugsachse.
Dafür müssen für eine asphärische Fläche folgende zwei Größen ermittelt werden:
- Die Ablage des paraxialen Krümmungsmittelpunktes zur Bezugsachse
- Der Winkel der asphärischen Symmetrieachse zur Bezugsachse
Die Ablage entspricht dem klassischen Zentrierfehler von sphärischen Flächen und wird in gleicher Weise mit dem elektronischen Autokollimator gemessen.
Für die Winkelmessung der asphärischen Linse wird ein zusätzlicher Sensor – bei TRIOPTICS der AspheroCheck® Sensor – benötigt. Er misst den Schlag am äußeren Rand der asphärischen Fläche.
Sind die Ablage und der Winkel der asphärischen Fläche bestimmt, können aus diesen Daten die folgenden Parameter errechnet werden:
- Abstand und Neigung der Asphäre bezogen auf die primäre Bezugsachse des Messsystems (entspricht der Drehachse)
- Abstand und Neigung der Asphäre bezogen auf die „optische Achse“ einer Einzellinse. Als „optische Achse“ wird die Gerade durch die Krümmungsmittelpunkte der sphärischen Anteile betrachtet
- Abstand und Neigung der Asphäre bezogen auf eine Bezugsachse nach DIN ISO 10110-6, wenn ein zusätzlicher Distanzsensor verwendet wird.
- Wenn eine Linse aus zwei asphärischen Flächen besteht: Winkel und der Abstand der beiden Asphärenachsen
Zentrierfehler von Zylinderlinsen und anamorphotischen Linsen
Zentrierfehler von Zylinderlinsen und anamorphotischen Linsen
Die Herausforderung beim Messen von Zylinderlinsen liegt in den unterschiedlichen Formen, in denen diese Linsen hergestellt werden. Sie unterscheiden sich sowohl in der Oberflächen- und Grundflächenform als auch in der Art der Fassung.
Typische Formen von Zylinderlinsen
Ähnlich wie sphärische Optiken werden Zylinderlinsen gemäß ihrer beiden optischen Flächen zunächst grob in Klassen eingeordnet. Man unterscheidet Linsen der Typen:
- Zylindrisch – Plan
- Zylindrisch – Sphärisch
- Zylindrisch – Zylindrisch
Am häufigsten werden Zylinderoptiken verwendet, die auf einer Seite plan bearbeitet sind, auch weil sich zylindrisch-plane Linsen messtechnisch besonders einfach charakterisieren lassen.
Mit den OptiCentric®-Systemen können aber auch alle anderen Zylinderlinsenformen und Objektive gemessen werden.
Da Zylinderlinsen keine Rotationssymmetrie um eine Achse aufweisen, ist auch die Außenkontur der Linsen häufig nicht rotationssymmetrisch. Dementsprechend wird darüber hinaus unterschieden in:
- Linsen mit rechteckigem Umfang
- Linsen mit rundem Umfang
Bei jeder Messung spielt der spezifische Linsentyp eine entscheidende Rolle. Je nach Ausführung der Zylinderlinse und Aufgabenstellung müssen unterschiedliche Sensoren und Auswertungsprogramme eingesetzt werden, um die Fertigungsgenauigkeit der Linsen zu überprüfen.
Zur Beschreibung des Zentrierfehlers von zylindrischen Linsen muss eine Bezugsachse gewählt werden. Dies kann beispielsweise eine Referenzkante am Glas sein, oder eine Fase an einer mechanische Fassung, in welche die Linse eingesetzt ist. Das nächste Unterscheidungsmerkmal zur Klassifizierung von Zylinderlinsen ist daher die Fassung
- Ungefasste Linse
- Gefasste Linse
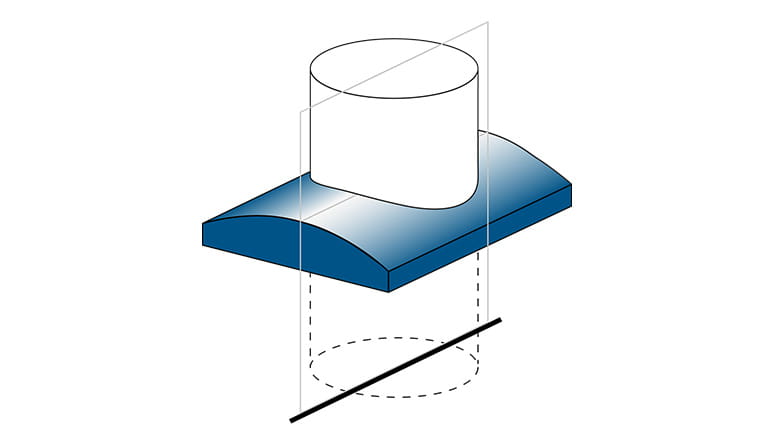
Messtechnische Herausforderungen beim Messen von Zylinderlinsen
Die Asymmetrie der zylindrischen Fläche macht die Qualitätsprüfung von Zylinderlinsen erheblich aufwändiger als die von sphärischen Optiken. Der Krümmungsmittelpunkt einer sphärischen Oberfläche ist eindeutig durch seine Lage definiert, die präzise bestimmt werden kann.Eine zylindrische Linsenfläche weist dagegen nur in einer Richtung einen Krümmungsradius auf. Der für sphärische Flächen typische Krümmungsmittelpunkt wird daher bei Zylinderflächen zu einer Linie, hier bezeichnet als Zylinderachse. Dies ist ein Grund, warum die Messung von Zylinderflächen aufwändiger ist als die Messung von sphärischen Optiken. Zur Auswertung dieser Zylinderachse muss nämlich neben ihrer Lage auch ihre Ausrichtung gemessen werden.
In Richtung der nicht gekrümmten Linsenoberfläche verhält sich eine Zylinderfläche wie eine Planfläche. Aus diesem Grund treten bei der vollständigen Charakterisierung aller Linseneigenschaften von Zylinderlinsen neben den von der sphärischen Optik bekannten Fehlern die typischen Fehler von Planoptiken auf.
Um die typischen Eigenschaften von Zylinderlinsen besser zu veranschaulichen, wird im Allgemeinen nicht von der Lage der Zylinderachse gesprochen, sondern von der Scheitellinie und der genauen Azimuthlage der Scheitellinien. Diese Linie entspricht der Zylinderachse, die entlang der optischen Achse auf die Linsenfläche projiziert wird.
Zentrierfehler bei optischen Flächen im Inneren eines montierten Objektivs
Zentrierfehler bei optischen Flächen im Inneren eines montierten Objektivs
Um Zentrierfehler einzelner optischer Flächen zu messen, wird der exakte Kippfehler bzw. die exakte Ablage des Krümmungsmittelpunkts von einer gegebenen Bezugsachse bestimmt. Einflüsse von optischen Flächen und Elementen, die vor der zu untersuchenden Fläche liegen, müssen durch optische Rechnung berücksichtigt werden. Dies gilt auch für die Zentrierfehler dieser Flächen, d. h. beginnend mit der ersten Fläche müssen die Zentrierfehler aller weiteren Flächen iterativ bestimmt werden. Mit den OptiCentric®-Systemen können typischerweise bis zu 20 Flächen von einer Seite vermessen werden.
Ein zweiter Messkopf wird bei den OptiCentric® Dual-Systemen verwendet, um den Zentrierfehler auch von der unteren Seite zu bestimmen. Somit können auch mehr als 20 optische Flächen erfasst werden.
Die sogenannte MultiLens-Messung liefert die exakten XYZ-Koordinaten aller Krümmungsmittelpunkte im Raum. Die gemessenen Daten werden bei der Analyse der Linse oder des Objektives verwendet und liefern zusätzlich folgende Ergebnisse:
- Berechnung der optischen Achse der Einzellinse(n)
- Ermittlung der optischen Achse einzelner Untersysteme oder der optischen Achse des Gesamtsystems
- Berechnung der Abstände und Winkel zwischen optischer Achse und Regressionsgeraden
- Berechnung der Lage von Einzellinsen oder Gruppen zu einer mechanischen Achse – hierfür ist zusätzlich ein Messtaster benötigt
Zentrierfehlerprüfung von Infrarotobjektiven
Zentrierfehlerprüfung von Infrarotobjektiven
Zum Prüfen von Einzellinsen und vollständigen Baugruppen, die nur im Infrarotbereich lichtdurchlässig sind, bietet TRIOPTICS speziell für die Wellenlängen der Infrarotbereiche entwickelte Messköpfe an. Typische Anwendungen sind z. B. das Prüfen von Linsen und Baugruppen für zivile und militärische Anwendungen. Insbesondere für den Einsatz in Wärmebild- und Restlichtsystemen werden Linsenmaterialien wie Ge, Si, ZnSe, ZnS oder CaF2 verwendet.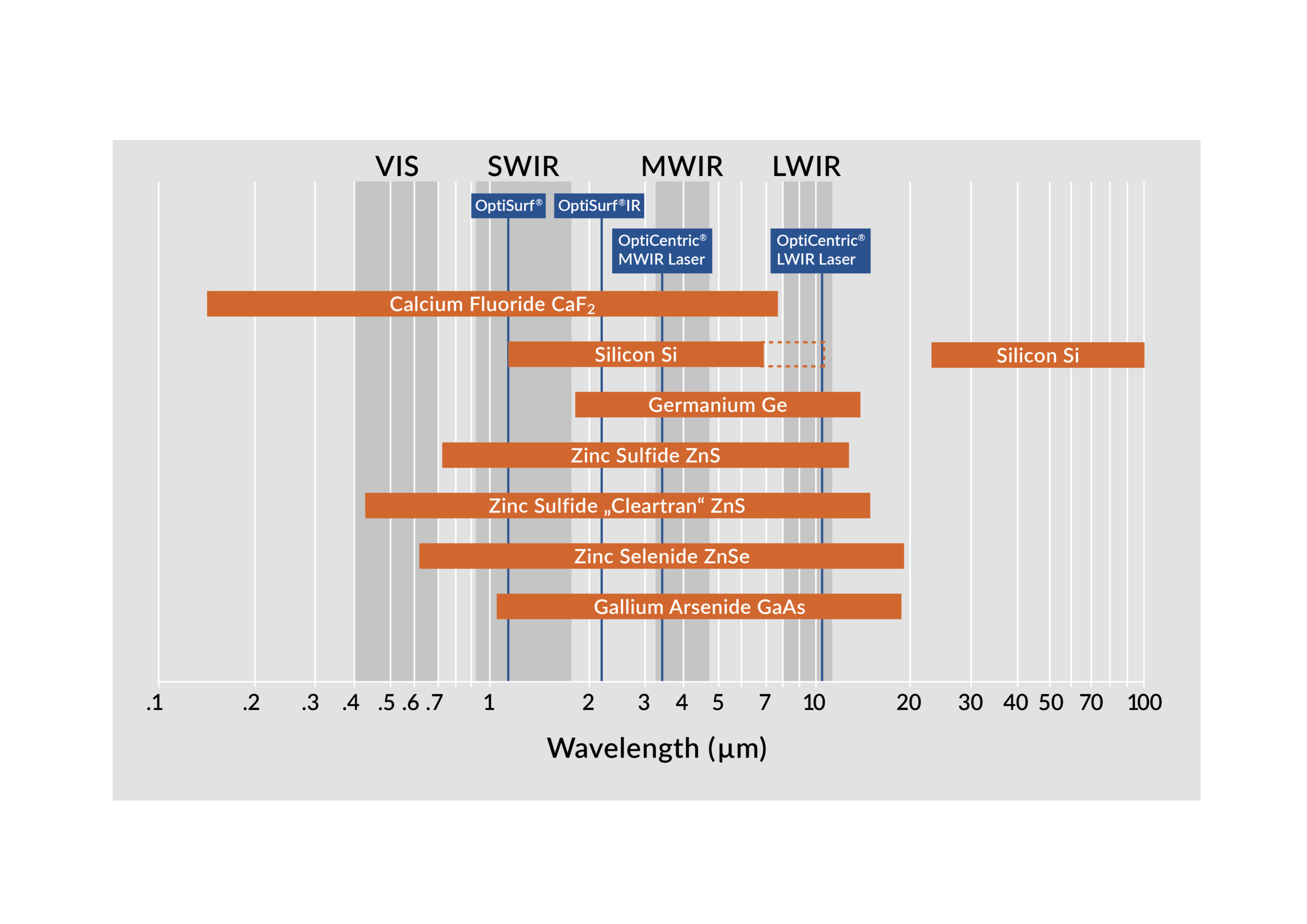
Infrarotbereiche
Die Infrarot-Wellenlängen sind für bildgebende Anwendungen in drei verschiedene Bereiche unterteilt. Innerhalb dieser Bereiche ist die Übertragung von Licht durch Luft sehr hoch. Dazwischen befinden sich stark absorbierende Bereiche im Spektrum.Die drei in der Bildgebung zum Einsatz kommenden Infrarotbereiche sind: kurzwelliges Infrarot (SWIR) mit Wellenlängen von 0,9 bis 1,7 µm, mittelwelliges Infrarot (MWIR) mit Wellenlängen von 3 bis 5 µm und schließlich langwelliges Infrarot (LWIR) mit Wellenlängen von 8 bis 12 µm. Da die Zentrierfehlermessung in Reflexion geometrische Informationen über das zu untersuchende Linsensystem liefert, ist die Wellenlänge der für die Messung eingesetzten Lichtquelle unabhängig von der eigentlichen Design-Wellenlänge der Optik. Anstelle dessen kann der geeignete Autokollimator anhand der Transmissionsbanden der verwendeten Materialien und der Oberflächenbeschichtungen ausgewählt werden.
Eine Übersicht über kompatible Materialien und die von den erhältlichen Messköpfen abgedeckten Bereiche bietet die nebenstehende Abbildung. Ein Sonderfall ist Silizium, da der lichtdurchlässige Bereich von der Stärke der Dotierung und vom Dotanden abhängt. Aus diesem Grund kann je nach Anwendung ein LWIR-Kopf geeignet sein.
Unterschiede zu VIS aus Sicht des Bedieners
Im Gegensatz zu VIS-Systemen ist das vom fokussierten Autokollimator ausgestrahlte Licht für das bloße Auge unsichtbar. Dies stellt jedoch beim Zentrieren des Prüflings kein Problem dar. Abgesehen davon unterscheiden sich die Geräte im Betrieb nicht von den VIS-Systemen, sodass Benutzer schnell für neue Wellenlängenbereiche geschult werden können.Unterschiede zu VIS aus technischer Sicht
Abgesehen von der Verwendung geeigneter Optiken und Lichtquellen in den Messköpfen besteht der bedeutendste Unterschied zwischen dem sichtbaren Bereich und dem Infrarotbereich vom technischen Standpunkt gesehen darin, dass im Infrarotbereich jedes Objekt, einschließlich des Prüflings, Licht in diesem Wellenlängenbereich ausstrahlt, sodass das Gerät den thermischen Hintergrund kompensieren muss, bevor eine Messung durchgeführt wird. Dies erfolgt automatisch durch die Software und erfordert keinen Eingriff durch den Benutzer. Außerdem ist der Kontrast zwischen Hintergrund und beleuchteten Bereichen geringer als im sichtbaren Bereich. Um die erforderliche hohe Auflösung zu erzielen, werden deswegen spezielle Bildbearbeitungsalgorithmen verwendet.Im Standard-Reflexionsmodus nutzt OptiCentric® die Rückspiegelung von der Linsenoberfläche. Daher hängt die Lichtintensität des reflektierten Bildes auf der Strichplatte stark von der verwendeten Beschichtung ab. Normalerweise sind alle Infrarot-Bildgebungslinsen AR-beschichtet. Allerdings variiert die Effizienz stark, was die Geräte, sofern möglich, durch Anpassung der Beleuchtungsstärke und der Verschlusszeiten kompensieren.
Im Allgemeinen ist die typische Genauigkeit der Zentrierfehlermessung ungefähr 1 µm, also etwas höher als bei VIS-Geräten. Dies ergibt sich durch die längeren Wellenlängenbereiche und die höhere Pixelgröße der in den Autokollimatoren eingesetzten Kameras.
Zentriermessung, Ausrichtung und Kleben von Linsen in Fassungen
SmartAlign für effizientes Ausrichten, Verkitten und Kleben von Linsen
Der SmartAlign-Algorithmus ist Teil der OptiCentric®-Software und sorgt dafür, dass die Linsen zu einer frei wählbaren optischen oder mechanischen Referenzachse ausgerichtet werden können. Je nach Fertigungsprozess wird die Referenzachse beispielsweise als optische Achse der unteren Linse eines Achromaten, als die Rotationsachse oder Achse eines Dorns definiert. Aufgrund dieser Flexibilität ist es möglich die OptiCentric® Cementing und Bonding Stationen auf unterschiedliche Fertigungsprozesse unserer Kunden anzupassen.Bonding 5D
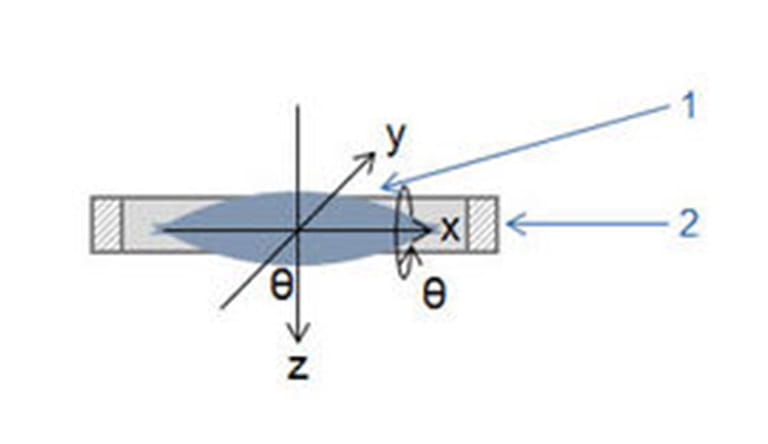
Bonding 5D
OptiCentric® Bonding 5D läßt eine Ausrichtung in fünf Freiheitgsgraden zu.
- 2 laterale Translationen
- 2 Verkippungswinkel (θx, θy)
- 1 axiale Translation (z)
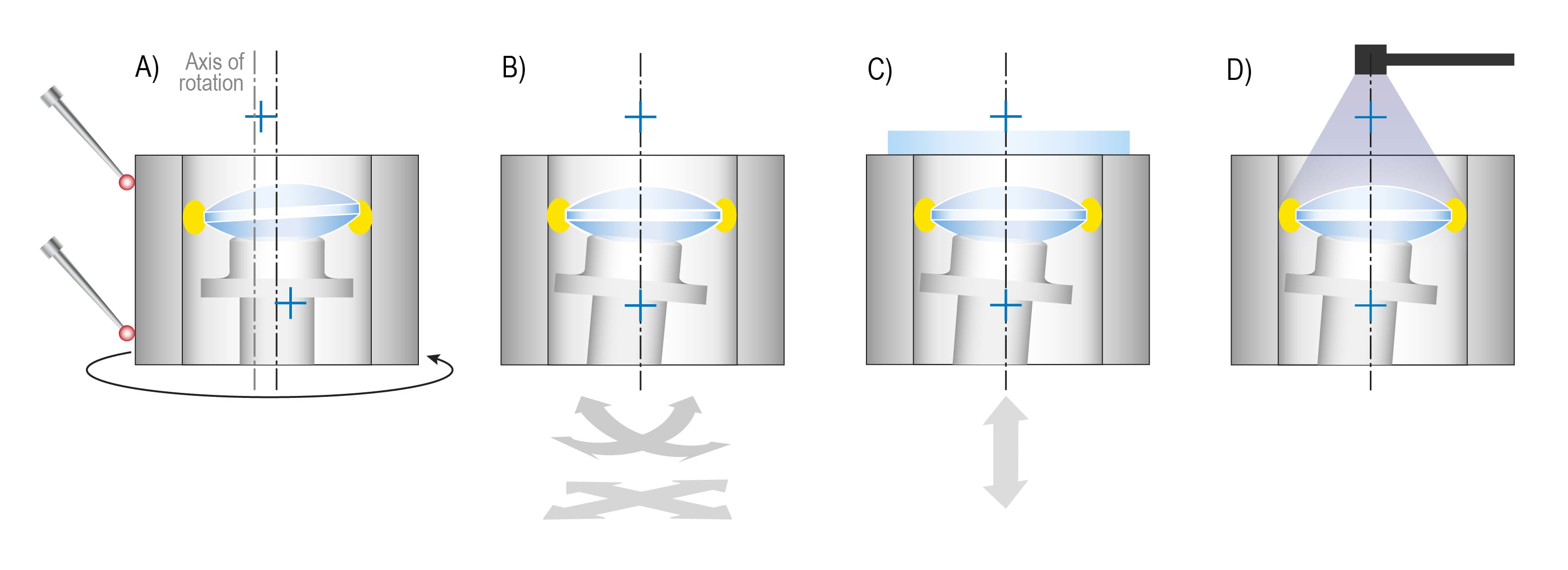
Verfahrensschritte bei OptiCentric Bonding 5D:
- Der Klebstoff wird aufgebracht und die Positionen der Achse n von Linse und Fassung werden gemessen
- Die Linse wird in der Fassung in vier Freiheitsgraden ausgerichtet: x, y, θx, θy
- Der axiale Abstand zwischen dem Scheitelpunkt der Linse und einer Referenzfläche wird gemessen und die Linse axial ausgerichtet
- Der Klebstoff wird ausgehärtet
Im Anschluss erfolgt das Aushärten des Klebstoffes, in der Regel mit UV-Licht. Hierbei sind natürlich die besonderen Klebstoffeigenschaften zu berücksichtigen, da sie Einfluss auf die finale Positionierung haben.
Mit OptiCentric® Bonding 5D ist der gesamte Prozess des Ausrichtens und Klebens automatisiert möglich. Hochpräzise Ergebnisse von < 1 µm in x, y, z Achse und < 2 arcsec in θx, θy sind bedienerunabhängig zu erreichen, mit vorhandenem Know-How sogar inklusive Klebstoffschrumpf. Das Verfahren eignet sich für alle Fassungsmaterialien und ist unabhängig von der Fassungsgeometrie. Hochflexibel lässt sich die OptiCentric® Bonding 5D schnell auf andere Prüflingsarten umrüsten. Diese Technologie ist auch besonders für Reinraumanwendungen geeignet.
Der neue Prozess erfordert ein Umdenken sowohl im Fertigungsprozess als auch im Design der Prüflinge. Auch wenn kein Rezess in der Fassung mehr benötigt wird, so kann er dennoch zur Aufnahme des Prüflings sinnvoll sein. Allerdings muss sichergestellt werden, dass die Linse nicht auf dem Rezess aufliegt, sondern um wenige Mikrometer darüber „schwebt“.
Unser Newsletter – Ihr Wissensvorsprung
Erfahren Sie als einer der Ersten von unseren Produktneuheiten und innovativen Anwendungsmöglichkeiten.